在庫管理術
製造業DXの課題や進まない理由、成功事例、DX推進ツール
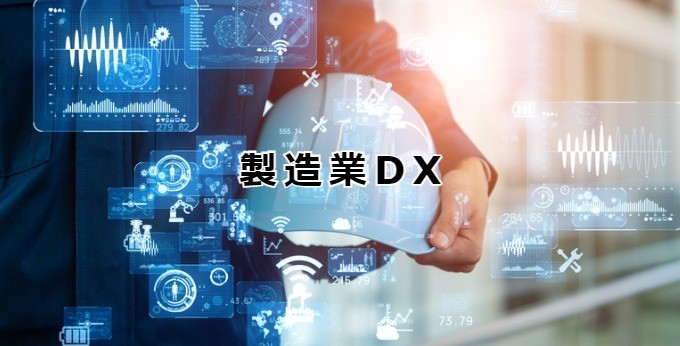
製造業のDXとは【分かりやすく解説】
DXとは、デジタルトランスフォーメーション(Digital Transformation)の略であり、デジタル技術による変革・変容を意味します。日本では経済産業省が2018年に「DXを推進するためのガイドライン」を提唱しました。
企業がビジネス環境の激しい変化に対応し、データとデジタル技術を活用して、顧客や社会のニーズを基に、製品やサービス、ビジネスモデルを変革 するとともに、業務そのものや、組織、プロセス、企業文化・風土を変革し、 競争上の優位性を確立すること
経済産業省のガイドラインではその他にも以下のようにも提唱されています。
「AI や IoT などの先端的なデジタル技術の活用を通じて、デジタル化が進む 高度な将来市場においても新たな付加価値を生み出せるよう従来のビジネスや組織を変革すること」
「デジタルデータを前提として新たな利益や価値を生み出すビジネスモデルへの移行。新たなデジタル時代にも十分に勝ち残れるように自社の競争力を高めていくこと」参照:経済産業省「デジタルトランスフォーメーションを推進するためのガイドライン」
参照:IPA「デジタル・トランスフォーメーション推進人材の機能と役割のあり方に関する調査」
製造業におけるDXとは、主に生産現場や周辺サプライチェーンでIoTやITを用いたデジタル技術で取得したデータを利活用し、生産ラインや組織体制を変革することです。この変革は単純なデジタル化や効率化を超えたものであることが期待されています。
つまり機械導入等による人日計算以上に、得られる効果・価値があることが前提となります。この際の効果・価値をDXを推進する上での明確な「目的」としなければ、膨大なデータが収集され続けるだけという落とし穴に陥りかねません。
製造業のDX【日本の場合】
日本の製造業におけるDXは、欧米で進められているDXと異なるものとして扱ったほうが良いとされています。その背景には、日本人の「モノづくり」や「製品の品質」に対する意識やモラルの高さ、各々の現場で何十年来も工夫を積み重ねた現場力の深さ・強味があります。
また、これまで個人の技術や経験値として蓄積されてきた「職人技」を属人化したり、技能継承者不在により消失させたりすることは、日本の製造業においては大きな損失です。一方、欧米のDXのロールモデルはほぼ完全な自動化を目指し、脱カーボンニュートラルにもかなり重心を置いた「スマートファクトリー」が理想とされています。
しかし日本では、デジタルを活用することで「職人技」を平準化し、個人のスキルが共有され、日本の製造技術力を活かすことがDXのカギと言われています。また現場力の高さ・深さを考慮するとファクトリーサイエンティスト*1は外部からではなく、現場をよく知る人間がデジタルを使いこなせるようになるほうがよいでしょう。
日本では、少子高齢化による労働力人口不足や、半導体不足・原油価格の高騰といった資材調達の問題、CO2排出量削減の提唱といったさまざまな課題があります。このような状況下においても、製造業でDXを推進させることは、将来にわたり継続する「日本の高い技術を誇るモノづくり」を行う土壌となります。
*1:蓄積・記録されたデータを分析し、新たな施策を運用する専門家
製造業のDXの成功事例
トヨタ自動車株式会社「工場IoT、トヨタIoT」
3D CADデータ*3や試作段階のデータは個々でデジタル化され、技術開発・生産ラインへの落とし込みに貢献してきたが、実際の製造時におけるデータの変容や顧客ニーズのデータの反映はタイムリーにフィードバックできていなかった。
そのため「工場IoT」、つまり工場の製造部門が所有するデータのネットワーク化から着手。これは効率や対費用効果重視の社風にもあったDX施策であった。
既存のデジタル化データを一元管理でき、各工場と各現場にまたがる情報共有の基盤としてセキュアな工場横断の共有プラットフォームを2~3年かけて確立。
さらにこれにあわせて、製造側は各社員がトヨタ生産方式*4に則り、デジタル技術を使った小規模なテーマを立案・実行し、効果を出すというボトムアップの取り組みを行い、人材の育成も併せて進めた。
結果として各事業所・工場でプラットフォームを使った現場プロジェクトを立ち上げ、プロジェクトの数をこなすことで、対費用効果が上がることが確認できた。この成果を受け、エンジニアリングチェーンやサプライチェーンを含むDX推進を打ち出しつつある。
*3:CAD:Computer Aided Design の頭文字をとったもので、直訳すると「コンピュータに設計を支援してもらう」という意味。紙の図面ではなくコンピュータを使って設計やデザインを行うこと全般を指す。3DCADとは、紙で行っていた2次元図面(2D)をコンピュータ上で3次元に拡張したもの。
*4:トヨタ生産方式:Toyota Production System、略称TPSで第二次世界大戦前後からルーツを持つ。トヨタ自動車が生み出した「ジャスト・イン・タイム」と「自働化」の2つの理念を柱に、資材の調達から製品の出荷段階までのムダを徹底的に排除し、製品価値を下げることなく生産を効率化する生産方式。海外ではリーン生産方式として知られている。
沖電気工業株式会社「バーチャル・ワンファクトリ」
背景としては、顧客要望を個別対応する必要性の高まりと、社会変化に伴う大量ロットの需要減に対する危機感から、工場間の横連携であたかもひとつの工場であるような生産方式をDX推進により構築できないかを検証。
各工場ごとに異なっていた、設計部門の図面等などの各種設計情報を共通化。具体的には、各工場の生産形態の特徴や製造に対する考え方、知見等を整理・把握した上で、工場間の融合を以下のように推進し、共通化された設計デ-タを各工場で受け取れるようにした。
|
工場間の連携により、技術・情報等の共通化だけでなく、相互の強みを活かした生産体制の構築が可能となった。さらに多品種少ロット生産の二ーズの取り込みや繁忙期の工場間の負荷分散など、外部環境変化への対応がより容易となった。
また2022年6月以降、さらなるDX新戦略として、4象限で「社会の大丈夫を作っていく」、全社に渡るDX・外部(顧客)へのDXソリューション・プロダクツモジュールの提供、DX戦略を4象限でマッピングし“わかりやすいDX”を統括する、を推進している。
株式会社今野製作所「ビジネスプロセス参照モデル」
事業戦略として、オーダーメイド型・高付加価値化へのシフトを検討したが、社内各部署において、個別受注への対応力不足が明らかになった。さらに小規模事業にも関わらず、さまざまな生産形態の混在や業務プロセスの複雑化など、製品と情報の整流化の必要性を感じていた。
NPO法人が普及推進している業務プロセスの分析ツール「ビジネスプロセス参照モデル」を活用して、業務の1つひとつの流れを整理・検証し、業務の可視化を行うDXを実施した。また業務プロセスの分析ツールを自社に合わせ小規模な開発を行った。
結果として、これまで“匠の技”を持つ職人と営業の力だけで事業が成り立っていたことが明確化され、製品・サービスの高付加価値化に向けより注力した設計段階を確立するきっかけとなった。
さらに設計業務と調達業務の間、在庫管理とエンジニアリングと販売管理の間など、部署間でデータを手入力により転記するプロセスがあることが判明し、必要なデータを自動流用する改善、DXの横展開へと至った。
生産形態を含め社内の整流化を行うことで、生産形態の特性に合った既存事業の位置づけの変革、従来手が出なかった新たなビジネスへの挑戦が可能となった。
製造業のDXに役立つツールをご紹介
製造業のDXを推進するためにさまざまなツールがありますが、自社の生産形態にあったツールであることはもちろん、知的財産・技術ノウハウなどの情報を保守するためにもセキュリティ面でも安全なツールが必要です。
それでは実際にはどのようなツールが導入されているのかをご紹介します。
生産管理システム|中小企業向け・セキュリティの高いシステムが多い
生産管理システムとはさまざまな生産現場において、納期・ロット数・工程数といった生産計画の管理を効率化させるシステムです。日本では「生産管理システム」自体を商品として扱う企業があり、代表的な企業だけでも20社近くに昇ります。
特徴としては、生産管理システムを自社開発する体力がない中小企業向けの商品が多く、また知的財産や技術ノウハウを保守するセキュリティの面でオンプレミス・パッケージソフト化された商品が数多く見られます。ただし、ここ最近ではシステムのアップデートやデータ保存容量の増設の利便性を上げるためにクラウド型のSaaSを提供する企業も増えてきました。
見積管理(新規見積・見積検索)から受注・生産準備・日報処理・工程進捗管理・出荷・売上・集計(原価や生産日報の集計)を一貫して行う生産管理に特化したシステムがベースとなっています。
それに加えて在庫管理や棚卸業務を加えたシステム、さらには債権管理・債務管理などの財務処理までもを加えたシステムがあります。また、パッケージ化されているとは言え、業務形態に合わせてカスタマイズ可能な商品があるようです。
データの収集方法に関しては、生産現場や倉庫から直接PCやタブレット・スマホ・IoT連携ツール・バーコードリーダーなどでリアルタイムに情報を収集・確認するのが一般的です。
BOMシステム|部品表を統一し、システム化された生産管理
ここ最近注目されているBOMシステムも、部品表(BOM)を基に、設計段階・製造段階・購買段階・保守段階などの各段階で統合されたシステムであり、主に機械・部品産業の生産管理に使用されています。
BOMシステムの導入には、同じ部品であるのに品番が異なったり、同じ組立作業であるのに設計図番号が異なったりということがないように、事前に部品の品番や設計図を洗い出し、事業所・工場間ですべて統一することが不可欠です。
BOMシステムを導入すれば、設計段階のE-BOMでは技術の蓄積や類似した設計図のBOMの流用・検索が容易になり、設計段階のMーBOMでは加工履歴の検索や設計者との連携がスムーズになるというメリットがあります。
また、購買段階であるP-BOMとM-BOMが同じシステム内で情報共有することにより、製造に必要な部品の調達進捗や生産の進捗が互いに把握できることで、生産リードタイムの短縮にも繋がるという点もメリットです。
しかしながら、在庫管理や棚卸、売上まで管理できるBOMシステムはない、顧客要望や市場ニーズが反映されにくい、というデメリットがあります。BOMシステムを生産管理に利用している企業は、その他の業務でDX推進するには別のシステム導入が必要となってくるでしょう。
RFIDシステム|トレーサビリティに優れ、データの上書きも可能
RFIDシステムとは電波領域を用い、情報の読み書きができるRFIDタグを活用し、タグを製品一つひとつに貼りつけることで、製品の生産段階から検品・出荷・店舗への納入・販売までの個別追跡に優れたシステムです。
RFIDタグは水や金属に干渉し読み取りエラーが起こることがありますが、液体対応のRFIDタグや金属対応のRFIDタグが開発され、さまざまな製造現場で用いられています。
特に自動車業界では20年も前からボディの生産ラインでRFIDシステムが利用されています。車体一つひとつにRFIDタグが貼りつけられ、リーダライタでスキャンすると今までの作業履歴や次の作業指示の閲覧が可能です。
また通常作業での完成品はもちろん、作業ミスや部品の欠損による、製品の手直しや廃棄などの情報が書き込まれ、製品一つひとつの作業履歴を追跡することができます。
RFIDシステムはそのまま在庫管理にも利用できます*5が、RFIDタグ自体、高性能であればあるほど高額となり、リーダライタ(スキャナタイプ・固定アンテナタイプ・ゲートタイプ)も20万円前後の価格となります。
金属対応や液体対応のタグの使用、継続したタグ購入、現場の各場所や資材の仮置き場・倉庫へのリーダライタの設置などを考えると初期投資だけでなくランニングコストも嵩ましされていくという点がデメリットです。
*5:後述に詳細あり。
ERPシステム|マルチカンパニー向けの統合基幹業務システム
ERPとは人的・物的・金銭的リソースを効率的に配分し、経営資源を有効活用するための企業理念のひとつです。この理念を実現化するためのシステムを「ERPシステム」もしくは「ERPパッケージ」と言い、生産管理だけではなくさまざまな部門(物流・販売から会計および財務・人事までの幅広い業務分野)にわたる管理システム機能を備えています。
ERPシステムは統合基幹業務システムとも呼ばれ、部門間にわたり情報を一元管理することが可能であるため、データのプラットホームと考えてもよいでしょう。また部署ごとに分散している業務システムを統合し、異なる部門の情報もリアルタイムで見える化できるのがメリットです。
どちらかというと、いくつもの製造業種、それに合わせた各販路を持つ商社、海外拠点などを含むマルチカンパニーに合ったシステムですが、近年では中小企業にも適したERPシステムが登場しています。
生産管理システムと同じようにERPシステムも商品としてパッケージ化され、セキュリティの面ではオンプレミスが多くみられていましたが、ここ最近ではクラウド型のSaaSも登場してきました。
ただし、さまざまな商品があるため自社に適したERPシステムの選択が難しいこと、サーバー構築費用や初期ソフトウェアの費用など初期投資がかかることや、それまで社内でさまざまな形態・品番・仕様書で分散していたデータを整理するのに企業規模によっては膨大な労力がかかることや、導入後のデータの扱いについてもルールの明確化・遵守の徹底管理をする必要があるという点がデメリットです。
在庫管理システム
過剰在庫や欠品、不良在庫などをなくすために在庫情報や入出庫情報などを入力し、正確な情報を把握・管理するための在庫管理に特化したシステム。さらに資材の納品から出庫・製品の仕上がりというモノの流れが見える化でき、一元管理が可能なシステムです。
生産管理システムを導入するのはハードルが高い、もしくは自社で培った生産管理システムがあり、在庫管理や棚卸だけ未だに目視確認や手書きの入出庫伝票に頼っているアナログな状態から抜け出せていない、という企業のDX推進に適しています。
在庫管理のツールとしては以下のような種類があります。
二次元コードにはQRコード・バーコードがあり、ハンディスキャナでひとつひとつ読み取る作業が必要です。QRコードは無料で作成できるアプリがあり、バーコードは既存のJANコードやITFコードを利用できるメリットがあります。
しかしながら、資材が納入された段階でQRコードを貼りつけたり、ひとつひとつスキャナでコードを読み取る手間があったり、またコードが汚れていたり、遮蔽されていると読み取ることができないというデメリットもあります。
それに対してRFIDシステムは電波の周波数帯域を利用したRFIDタグを使用し、遮蔽されにくい性質を持つため複数タグを一括で読み取れるという特長があります。バッテリー内臓のアクティブ型や外部の電磁波を動力源とするアクティブ型の利用により、タグ自体の寿命が長いのもメリットです。
さらに専用のリーダライタによりデータの読み書きができるので、生産段階から検品・出荷・店舗への納入・消費者の購買まで履歴の書き込みが可能。そのため、製品の個別ごとのトレーサビリティにも優れています。
ただし、倉庫にわざわざ赴いて製品一つひとつにタグを貼る、リーダライタでスキャンするという手間は残り、またタグやリーダライタ・上位システムの導入コストが比較的高いという点がデメリットです。
最後に重量センサですが、これは重量センサと管理したいモノを上位システム内で紐づけさえしておけば、重量センサに載せるだけでOK!タグ貼りやスキャンは一切不要で、重量により正確な個数や割合をカウントします。
さらにスマホやタブレットに対応しているアプリで入出庫管理ができるため、わざわざ倉庫や資材の一時仮置き場に行くことなく、モノがどのように流れているか遠隔での一元管理が可能です。
専門のコンサルタントに依頼する
製造業のDXにはそれに特化したコンサルタントを行う企業が数多くあります。
コンサルティングの各企業に共通するのは、まずアナログ的な手段をデジタル化する前に、既存の業務内における課題を洗い出し、またデータを活用するためにどのようなシステム連携を採ればよいか、部門間でバラバラに管理されがちなデータの統一化などの基盤づくりからスタートする手法が採られている点です。
DX推進するために、何をどうしたらよいか判らない、課題がありすぎてどれから手を付けたらよいか判らない、DX推進に割ける人的リソースがない、といった企業がコンサルティング会社に依頼することが多く、製造業のDXに特化したコンサルティング企業も年々、増えてきています。
製造業DXの課題【進まない理由・失敗例】
製造業DXの課題
製造業のDXを推進するためには、製品開発から製造現場、顧客対応などさまざまな部署で採用されている手段をアナログからデジタルに移行するだけでなく、統括的なデジタル化によって、各部署の形態を変革するのが不可欠です。
そのためには、組織内のデータ共有化や同じモノでも事業所や設計者によってバラバラになりがちな品番・仕様書・作業標準書の統一化など解決すべき課題が数多くあります。
また、熟練工やベテランの営業マンであればあるほど、自己の技術ノウハウや個人の信頼による販路を持ち、スキルや情報の共有化に難色を示しがちです。そこで将来の競争を勝ち残っていくためにも、DXの重要性やスキル・情報の共有化が「当然のこと」として受け止められる社内風土を作っていかなくてはいけません。
さらにDX推進にあたり、実際のデータ処理作業やIoTツール・検知センサー・AIの使い方を学ぶ人材育成も必要となってきます。このようなさまざまな課題を事前に一つひとつ解決していかないと、DX推進が失敗に終わる可能性もあります。
製造業のDXの進まない理由・失敗しがちな例
製造業のDXが進まない理由としては、上述の課題を解決する体力やマンパワーが企業にない、もしくは経営判断ができない、という声があります。
詳しく調べると、日本企業の営業利益率と企業行動の関係の分析では、製造業における2017年度から2020年度の平均値で、営業利益率が低い企業では、設備投資は少ないが借入金増加率が高いという報告があり、中小企業や営業利益率の低い企業はDXに投資できないという現実問題が浮き彫りになってきます。
さらにデジタル投資によってビジネスリターンが得られないリスクを感じている、平時の効率性や生産性を重視して旧来の基幹システムの更新や保守を志向し、新たなデジタル投資に背極的でない、さらにはDX推進に関わる人材不足という背景もあり、これらが製造業のDXが進まない理由として考えられています。
またDXの失敗例としては、自社の生産形態(大量生産に限らず、多品種小ロットや個別生産方式・繰返生産方式)にそぐわない生産管理システム*6を導入したり、ある程度はマッチしているもののカスタマイズしようとすると予想以上の追加料金が必要であったり、そもそも社内風土が未だにDXを進める土壌が出来上がっておらず、現場からの反発があったりという事例が挙げられます。
*6:前述の「製造業のDXを推進するツールとは?」に詳細を記述
スタートアップのほうが成功しやすい
さまざまな観点から製造業のDXは急務と考えられますが、なかなかDXの推進に踏み切れない企業も多いようです。特に旧態依然とした中小企業よりは、近年スタートアップした企業のほうが社風や従業員の考え方に柔軟性があり、DXの成功例が目立ちます。
ただし日本の製造業・生産方式のルーツと言っても過言ではない「トヨタ」や、半導体のトップメーカー「キオクシアHD」、AI技術をベースにマルチカンパニーに成長した「OKI」などの大企業は比較的早い時点でDX推進の舵を取り、さまざま製造業DXの見本となっています。
あらゆる課題を早急に解決する危機感を持ち、不測の事態に対する柔軟性を重視し、ビジネス変革や人材育成においてIT投資を志向する経営手腕を持つ企業が今後もさまざまなDXを行っていくことでしょう。
在庫管理DXを推進する「スマートマットクラウド」
現場のあらゆるモノをIoTで見える化し、発注を自動化するDXソリューション「スマートマットクラウド」を使えば、タグやコードの手貼り・スキャンなど一切不要!よりカンタンな在庫管理の自動化が可能となります。スマートマットの上に管理したいモノを載せるだけで設置が完了*7。
あとはマットが自動でモノの在庫を検知、クラウド上でデータを管理し、適切なタイミングで自動発注してくれるため、製造ラインを止める原因である欠品を防いだり、在庫量の推移をグラフ化できるので、過剰在庫や滞留在庫の見える化にも有効です。
さらに、スマートマットクラウドは生産工程のモノ・情報の整流化にも効果的。例えば「かんばん方式」での仕掛品置き場に重量センサを置き、仕掛品の数量を管理すると、仕掛品が滞留していれば後工程の遅延、欠品していれば前工程の遅延など、ひと目で工程ごとの進捗を可視化できます。
また組立製造で数多く活用されている「配膳作業」の管理にもスマートマットクラウドは有効。各配膳内容と重量センサを紐づけておけばよりスムーズで的確な作業が可能で、コミュニケーションコストをかけることなく、補充待ちによる生産遅延を防ぎます。
*7:モノの名称・品番・1個あたりの重量・100%重量などを上位システムに紐づけできる。
「スマートマットクラウド」による在庫管理DXの効果とは?
在庫管理にスマートマットクラウド(SMC)を導入すれば、在庫管理のDXが推進され、以下のような効果が得られます。
人為的ミスの削減・人的負担の解消
目視で在庫を数え、エクセルなどにデータを手入力するアナログな手段はもとより、同じくDXと言っても、二次元コードやRFIDシステムはコードやタグを手貼したり、ハンディターミナルやリーダライタでスキャンしたり、人力による作業が必然的に多くなります。
それに比べて重量により数を正確にカウントする「スマートマットクラウド」では、管理したいモノを重量センサに載せるだけでOK。人力による作業を大幅に減らせるだけでなく、数え間違い、重複読み込みといった人的ミスも大幅に削減できます。
在庫が保管されている倉庫や一時仮置き場に、本業の合間にわざわざ足を運んで数える・スキャンする必要もなく、リアルタイムの在庫情報を手元のPCから一元管理することが可能です。
在庫・棚卸業務にかかわる労働コストや時間を削減する「スマートマットクラウド」。数え間違いなどのミスによる心的ストレスや、どこに何があるかどうしても属人化してしまいがちな在庫管理を解消します。
*8:一定の重量(個数・%)以下になれば自動発注・発注アラートを出す閾値を決めることが可能
*9:発注残や高回転発注にも対応した高度な自動発注システムを搭載
◆特長
- コードやタグの手貼り不要・スキャン不要で人的負担を軽減
- 心的ストレスやヒューマンエラーの軽減
- リアルタイム&遠隔での一元管理が可能
- 在庫管理の属人化の解消
在庫の適正化と機会損失を防ぎ、売上の最大化が可能
適切なタイミング*8で自動発注、もしくは発注アラートをかける高性能な自動発注システムにより、生産ライン停止に繋がりかねない欠品*9や、重複発注による過剰在庫*9の防止にも繋がります。
また在庫量のデータ推移グラフにより適正在庫を分析し、滞留在庫や過剰在庫を防ぎます。さらにリアルタイムの在庫量が一元管理できるので、棚卸業務にかかる労力や時間も大幅に削減。工場の操業を停止して棚卸をする必要はもうありません。
在庫のムダを省き、「必要なときに、必要なものを必要な分だけ」というJITの理念に基づいた在庫管理を可能にします。
◆特長
- 資材の欠品による製造ラインに影響が出ることを防ぐ
- 適正在庫を維持することで、在庫圧縮によるコストカットに成功
- 棚卸業務のために操業の停止など、機会損失を防ぐ
- 必要なときに、必要なものをのJITの理念に則った在庫管理が可能
「SMC Handy App」 でさらにカンタン在庫管理
スマートマットクラウドのアプリ「SMC Handy App」を使えば、スマートマットに在庫を載せる・取るときにスマートフォンのカメラでバーコードを読みこんで、在庫情報を現場でサッと登録できます。商品にバーコード情報があれば、有効期限やロット情報も簡単に登録できるようになりました。
スマートマットクラウドの初期設定も「SMC Handy App」があればクイックに完了。スマートマットのシリアルIDをカメラで読み込むだけで、簡単にマットと在庫の紐付け登録ができます。
◆Handy Appの機能
- 棚卸:在庫残量確認・マットと紐付けていない在庫の残量登録
- 出荷処理:担当者、出荷先、在庫の出荷数の登録
- 入荷処理:担当者、在庫の有効期限・ロット情報ごとの入荷数の登録
- スマートマットクラウド初期設定:在庫情報とスマートマットIDの紐づけ
「スマートマットクラウド」による工程カイゼンDX効果とは?
スマートマットクラウドはリアルタイム実在庫の見える化により、工程カイゼン・DXを進めるIoT SaaSプロダクトとしても活用できます。IoTで現場のモノの動きを捉え工程内のモノの流れを分析し、工程間の問題を見える化します。
スマートマットクラウドはリアルタイム実在庫データを武器に工程を跨ぐ流れの澱みを特定し、原因追及をより簡便にするため、現場力の向上に寄与します。
つまり製造現場や在庫置き場・倉庫に直接、出向くことなく管理画面からリアルタイムの部品・仕掛品の在庫数を確認できるため、生産スケジュール遅延の早期発見や補充タイミングの把握ために倉庫や工場内を走り回る必要はもうありません。
さらにスマートマットクラウドは生産工程ごとの進捗状況も可視化できるDXソリューションです。前工程に必要な部品を、どのタイミングでいくつ必要かをリアルタイムかつ自動で伝えることができます。それにより互いにコミュニケーションコストをかけることなく各工程の進捗度合いや澱みを可視化し、生産プロセスに潜むさまざまな課題の問題解決に繋がります。
◆特長
- 遠隔で在庫を一元管理::倉庫や各拠点の在庫を管理画面で一元管理
- 需要に見合った供給を実現:ひとつ前の工程に伝え、過不足なく生産できる
- 生産効率を最大化:リアルタイムかつ自動で伝え、ムダがない
- コミュニケーションコストの削減:互いの進捗度合いをリアルタイム把握可能
「スマートマットクラウド」の機能詳細
さまざまな自動発注に対応
お客様の発注先に合わせた文面でメール・FAXの送信が可能です。
在庫圧縮を促進
推移を把握できるグラフで適切な在庫量を判断し、在庫圧縮を促進します。
置く場所を選びません
スマートマットはA3サイズ〜A6サイズまでの4サイズ展開。ケーブルレスで、冷蔵庫・冷凍庫利用も可能。
API・CSVでのシステム連携実績も多数
自社システムや他社システムと連携を行い、より在庫管理効率UPを実現します。
リアルタイム実在庫のデータを収集、分析、遠隔管理が可能
スマートマットクラウドはリアルタイム実在庫のデータを収集、分析、遠隔で管理。工場内の自動化、スマートファクトリー化をサポートするIoTソリューションです。
IoTで現場のモノの動きを捉え在庫管理を自動化、その上で工程内のモノの流れを分析し問題を見える化します。さらにリアルタイム実在庫データを武器に工程を跨ぐ流れの澱みを特定しDX、現場力の向上に寄与します。
在庫置場に出向くことなくリアルタイムで管理画面から部品と仕掛品の在庫数を確認できます。在庫確認や補充タイミング把握のため、倉庫や工場内を走り回る必要はもうありません。
スマートマットクラウドは生産工程の進捗状況も可視化。
後工程からひとつ前の工程に、必要な部品を、必要なタイミングで、いくつ必要かを自動で伝えることで、製造業の生産プロセスに潜むさまざまな課題を解消します。
AI x IoTで在庫最適化をし続けられる
スマートマットは、最新データ(入出庫の理論値ではなく、現場の実数データ)を溜め続けます。
そして、その大量データをAIが監視・解釈・検知。問題をタイムリーに抽出して改善を提案するので、常に在庫の最適化をし続けることができます。
スマートマットクラウドで在庫管理DX化を実現した製造業の導入事例
▼毒劇物管理のDXを推進(三菱ケミカル株式会社)
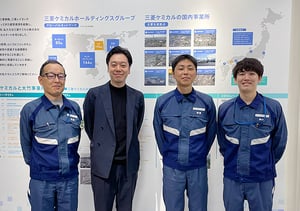
生産性向上に繋がる現場DXを模索しており、スマートマットクラウドを導入。デジタル移行に留まらない現場で結果がでるDXとして評価を獲得。
続きを読む>>