在庫管理術
【図解】ジャストインタイム(JIT)【意味・歴史・考え方と三原則・目的・事例・デメリット・在庫を適正化しコスト削減するIoT】
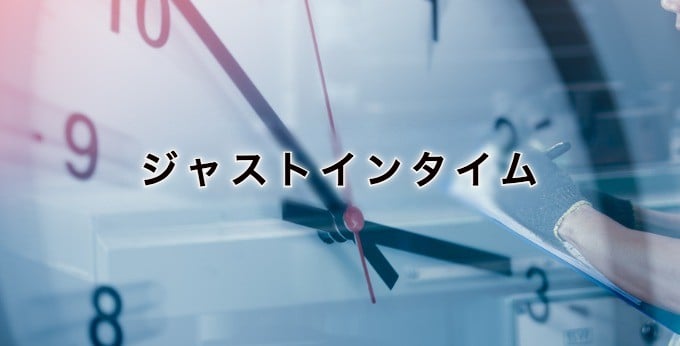
この記事では、製造業をはじめ、さまざまな現場で導入されているトヨタ生産方式の柱の1つであるジャストインタイムの目的やメリット、カンバン方式との違い、ジャストインタイム物流、事例、デメリットについてわかりやすく解説します。
\耳から学ぶ👂ポッドキャスト/
🎵音が流れます
ジャストインタイムとは【意味・歴史】
ジャストインタイムとは、「必要なものを、必要な時に、必要な量を生産することで、在庫を徹底的に減らして効率化すること」。製造業や物流業界などの現場で用いられている生産方式のひとつです。
別名、ジャストインタイム生産方式とも言われています。
そのルーツや歴史は、トヨタ自動車の創業者(2代目社長)である豊田喜一郎氏が合目的経営の観点から導入したトヨタ生産方式にあります。
トヨタ生産方式は、自働化とジャストインタイムという2つの考え方を柱として確立されてきました。
※ トヨタではニンベンの付いた「働」の漢字を使用
生産工程とジャストインタイム
生産工程とは、原材料が加工され製品完成するまでの生産活動の進行過程のこと。やるべきことが順番に何段階も分かれています。大量生産の場合、工程ごとに人員を分けることで、
- 作業員1人の作業スピードが早くなる → 作業の習熟度が高まり、ミスが減る
- 途中の仕掛品を前もって作っておける → 工程の時間を削減できる
といったメリットがあるため、生産効率を高めることができます。さらに生産効率が高まることで、
- 単位時間で生産できる量が増える。機会損失がなくなり売り上げアップ
- 1つあたりにかかる人件費が下がる。コストが安くなるので利益が上がる
というメリットも生じます。大量生産を行う製造業において、生産工程を管理し生産性を高めることは大変重要であり、そのために生まれた仕組みがジャストインタイムというわけです。
ジャストインタイムの前提
ジャストインタイムの前提として、平準化(へいじゅんか)があります。
平準化とは、製造業において、「量」や「種類」を均等にばらして生産する手法の一つ。平準化生産は、いつでも一定に生産量や生産品目が流れ続けている状態をあらわします。
トヨタ生産方式のジャストインタイムは、この平準化生産ができていることが前提となります。
ジャストインタイムの考え方・三原則
ジャストインタイムの考え方は、生産現場の3Mであるムダ・ムラ・ムリを徹底的になくし、良いものだけを効率良く造ることです。
注文のあった製品・商品を、より早く届けるために、以下の流れで最も短い時間で効率的に造ります。
- 受注したら、なるべく早く生産ラインの先頭に生産指示を出す
- 組立ラインは、どんな注文がきても造れるように、全ての種類の部品を少しずつ取りそろえておく
- 組立ラインは、使用した部品を使用した分だけ、その部品を造る工程(前工程*)に引き取りに行く
- 前工程では、すべての種類の部品を少しずつ取りそろえておき、後工程*に引き取られた分だけ生産する
*前工程・後工程:ものをつくる順序を意識した場合に使われる工程の呼び名の1つ。連続した2つの工程において順序が先の工程を前工程という。それに対して、順序が後の工程を後工程という。
そして、上記の内容を簡潔にまとめたものをジャストインタイムの三原則とよんでいます。
- 後工程引き取り
- 工程の流れ化
- 必要数に応じてラインタクト*を決定
*ラインタクト:1つの製品(同一品種)を造るのにかかる時間
ジャストインタイムの目的
ジャストインタイムが導入される前の製造業では、1910年代にアメリカのヘンリー・フォードがつくりあげたと言われる流れ作業の大量生産方式が主流でした。
しかし、大量生産方式には、急な市場のニーズの変化に対応ができないため機会損失や過剰在庫といったリスクがあったため、考え出されたのがジャストインタイム生産方式です。
ジャストインタイムの目的をわかりやすく簡単にまとめると
- 停滞を解消する際の考え方・指針
- モノ・情報が停滞なく流れていくために1つずつ問題を解消していくこと
となります。
ジャストインタイムのメリット
「必要なものを、必要な時に、必要な量を生産することで、在庫(経費)を徹底的に減らして効率化する」ジャストインタイムは、市場環境の変化に柔軟に対応できるため、以下のようなメリットが生まれます。
- 在庫の適正化(過剰在庫や余剰在庫の削減)
- 管理コスト削減(保管スペースや光熱費、在庫管理費、人件費の削減)
- 販売機会損失の防止
- リードタイムの短縮
ジャストインタイムとカンバン方式の違い
ジャストインタイムとよく比較されるかんばん方式は、同じくトヨタ自動車が開発した生産方式です。
具体的には、製造する商品には「かんばん」と呼ばれる商品管理カードがあり、商品名・品番・保管場所など詳細な情報が書かれています。
そして、このかんばんの指示通りに生産することで無駄がなくなり、その後の工程もかんばんを確認することで詳細を把握できるという仕組みです。
2つの違いを簡単にまとめると…
カンバン方式は、ジャストインタイムを達成するためにトヨタが作り上げた独特の生産方式であり、手段。わかりやすく言えば、ジャストインタイムが目的で、かんばん方式はその道具と言えます。
ジャストインタイム物流
主に製造業の現場で用いられているジャストインタイムですが、物流の現場でも「ジャストインタイム物流」と呼ばれ、広く導入されています。
ジャストインタイム方式を応用した「必要なものを、必要な時に、必要な量だけ届ける」配送システムです。
ジャストインタイム物流には、次のようなメリットがあります。
- 生産現場での在庫削減
- 作業効率アップ
- 在庫保管スペースの有効活用
- 管理コストの削減
ジャストインタイムのデメリット・問題点
ジャストインタイムには大きなメリットがある反面、以下のようなデメリットがあるとも言われています。
-
在庫切れ・在庫不足
必要以上に在庫を持たないので、災害や天気、新型コロナといった不慮の事態の際に在庫切れ・在庫不足により、生産が止まってしまう危険性も。
コロナ渦で原材料となる半導体不足が大きな問題になった一因として、部品メーカー各社がジャストインタイムによる在庫管理に依存しすぎたため、という意見も上がり、ジャストインタイムを見直す必要性も検討された。
-
下請け業者へのしわ寄せ
在庫を徹底的に削減するため、その都度生産するので、必要な部品や資材を大量発注することがなく、下請け業者がその都度納入する必要がある。
人件費や運搬費、部品や資材の在庫保管費などが負担になることもあり、「下請けいじめ」と揶揄されることも。
-
導入コスト
カンバン方式の仕組みを構築したり、工程の流れ化などジャストインタイムの三原則を新たに構築するためのコストがかかるため、中小企業には不向きと言われている。
人的ミスの発生等かんばん方式の運用がうまくいかない場合、IoT活用による生産管理の自動化が効果的です。
IoT活用でジャストインタイムを実現
IoTは、センサーが搭載されており、モノの状態や周辺環境といった情報を感知・収集し、インターネットを介して、それらのデータを人やモノに伝えます。
当社の在庫管理システム「スマートマットクラウド」も、重量センサを活用したシステムです。重量センサを搭載する工程管理・在庫管理IoTソリューション「スマートマットクラウド」の機能を紹介します。
スマートマットクラウドで工程改善。モノの流れをスムーズに
IoTで在庫管理を自動化、工程カイゼン・DX推進
スマートマットクラウドはリアルタイム実在庫の見える化で在庫管理、工程カイゼン・DXを進めるIoT SaaSプロダクトです。IoTで現場のモノの動きを捉え在庫管理を自動化、その上で工程内のモノの流れを分析し問題を見える化します。さらにリアルタイム実在庫データを武器に工程を跨ぐ流れの澱みを特定しDX、現場力の向上に寄与します。
在庫置き場に出向くことなくリアルタイムで管理画面から部品と仕掛品の在庫数を確認できます。在庫確認や補充タイミング把握のため、倉庫や工場内を走り回る必要はもうありません。
スマートマットクラウドは生産工程の進捗状況も可視化。
後工程からひとつ前の工程に、必要な部品を、必要なタイミングで、いくつ必要かを自動で伝えることで、製造業の生産プロセスに潜むさまざまな課題を解消します。
◆特徴
- 遠隔で在庫を一元管理:倉庫や各拠点の在庫を管理画面で一元管理
- 需要に見合った供給を実現:ひとつ前の工程に伝え、過不足なく生産できる
- 生産効率を最大化:リアルタイムかつ自動で伝え、ムダがない
スマートマットクラウドでジャストインタイムを実現した事例