在庫管理術
タクトタイム【計算方法・標準作業の3要素・サイクルタイムやリードタイムとの違いと関係性】
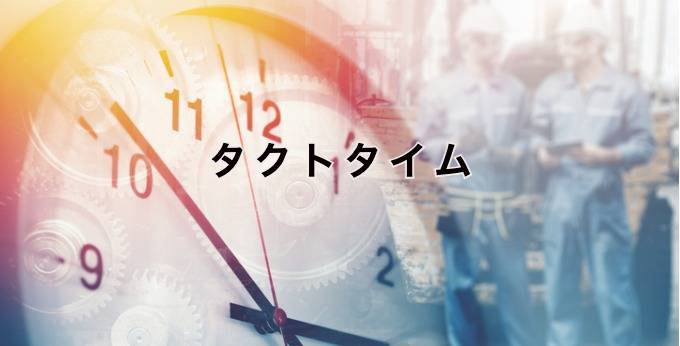
タクトタイムとは
タクトタイムが短ければ短いほど、稼働時間に対してより多くの製品を生産することができるため、工場の製造ライン能力のバランスを整え、効率化を図るために重要視されている数値です。
この記事では、タクトタイムの計算方法、標準作業の3要素、サイクルタイムやリードタイムとの違いと関係性についてわかりやすく解説。
タクトタイムとサイクルタイムのバランスを維持し、生産ラインの効率化を図るIoTソリューションもご紹介します。
目標タクトタイムの計算方法
タクトタイムは以下の計算式で求められます。
タクトタイム=1日の定時稼働時間÷1日の生産必要数
タクトタイムの計算には、1日の定時稼働時間(稼働時間から休憩時間などを引いた時間)が必要です。
タクトタイムの計算をする際に、この定時稼働時間をしっかり算出しないまま計算してしまうというミスが起こるため、注意しましょう。
タクトタイムの計算例として、稼働時間が8時間で、生産必要数(売れる数)が1000個の場合、
8時間 (480分)÷1000=28.8
タクトタイムは28.8秒になります。これは、1つの製品を28.8秒で作ることが目標値ということになります。
トヨタ生産方式におけるタクトタイム
トヨタ生産方式では、人の動き・モノ・設備の最も効率の良い組合せを考え、良い品物を、より早く、安全に、ムダなく造るための作業方法のことを標準作業と呼んでいます。
そして、その標準作業は、「タクトタイム」、「作業順序」、「標準手持ち」の3要素から構成されます。
タクトタイム
毎日の生産の中で製品1つを「何秒で造らなければならないかという時間」のこと。
作業を行なう際の1サイクルの時間(サイクルタイム)を、このタクトタイムに合わせ、同等にしていくことが改善のスタートとして重要に。
トヨタ生産方式では、実行タクトタイムという言葉も存在します。
タクトタイムは通常、定時生産で計算するのに対し、やむを得ず残業を含んで生産する場合の製品1つの造るべき時間を実行タクトタイムと呼んでいます。
作業順序
材料から製品が完成するまでの工程において、作業者がモノの運搬、機械への取付け取外し、加工・組立等の作業を「最も効率的に行なう」ための順序のこと。
標準手持ち
同じ手順で繰返し作業が出来るための必要最小限の手持ち(工程の途中にある仕掛品)のこと。
工程間での途切れや淀みをなくし、各作業をスムーズにつなぐために必要です。
標準手持ちが、決められた数量よりも多くなっていると、生産に異常があるとされます。
このような標準作業を行う目的は、製造現場のルールの明確化です。
トヨタの「標準基準の目的」という中にある言葉「標準のないところに改善はない」というように、標準を決めることから改善が始まります。
サイクルタイム、リードタイムとは?タクトタイムとの違い
製造現場で使われるよく似た用語にサイクルタイム、リードタイムがあります。
|
|
タクトタイム | ひとつの製品を製造するのに必要とする時間。 |
サイクルタイム | 1つの製品を製造する際の工程開始から完了までの1サイクルに実際にかかる時間。 |
リードタイム | 製品の発注から納品までの一連の工程にかかる時間。 |
それぞれをわかりやすく、タクトタイムとの違いを簡単に説明すると、
サイクルタイム
1つの製品を製造する際の工程開始から完了までの1サイクルに実際にかかる時間のこと。
サイクルタイムは、純粋に製造にかかる時間なので、途中で行われる品質チェックや機械の管理などにかかる時間は含まれません。
サイクルタイムは、以下の計算式で算出します。
サイクルタイム=1日の定時稼働時間÷1日の実際の生産数
今、現在の自社生産設備で製品1個を生産するのにかかる時間を表します。
つまり、タクトタイムとサイクルタイムの違いは、
●タクトタイム
顧客から依頼された生産数を製造するためには、1個あたり何秒で生産できるかを算出した時間で、顧客目線。
●サイクルタイム
現状の自社生産設備で製品1個を生産するのに実際にかかる時間を算出。自社(生産側)目線。
リードタイム
製品の発注から納品までの一連の工程にかかる時間のこと。
製造業においては、「手番(手配番数)」「先行日数」「基準日程」と同じ意味合いで使われる言葉です。
つまり、タクトタイムとリードタイムの違いは、
●タクトタイム
必要生産数をもとに、どれくらいの時間で1つの製品を作れば良いのかを算出した時間。
●リードタイム
製品1つを作るのにかかる作業時間だけでなく、製品の発注から生産・納品すべての工程にかかる所要時間。
リードタイムは、製造工程全体の予定を決める上で欠かせない数値です。
*リードタイムに関する詳細は以下の記事も参照。
リードタイム×物流|リードタイムの種類や数え方と短縮の方法
発注リードタイム【特徴・改善方法とそのメリット・製造納品工程リードタイム・短縮をサポートするIoT機器】
タクトタイムとサイクルタイムの関係性
タクトタイムとサイクルタイムの関係性から以下のことがわかります。
サイクルタイム=タクトタイム
サイクルタイムとタクトタイムが同等の時間。無駄なく生産ができている状態。
サイクルタイム>タクトタイム
サイクルタイムが長く、タクトタイムが短い。生産が追いついていないため、欠品や納期遅延の危険性がある状態。
サイクルタイム<タクトタイム
サイクルタイムが短く、タクトタイムが長い。目標(顧客のニーズ)より早めに多く生産しているため、過剰在庫の危険性がある状態。
タクトタイムとサイクルタイムは、生産ラインの業務効率化・生産性向上のために欠かせない指標です。
そして、タクトタイムとサイクルタイムはなるべく同じ数値であることが望ましく、どちらかが長くても短くても問題が発生してしまうということになります。
タクトタイムとサイクルタイム、両方のバランスをしっかり考慮することが重要です。
サイクルタイム=タクトタイムで無駄のない生産を実現「スマートマットクラウド」
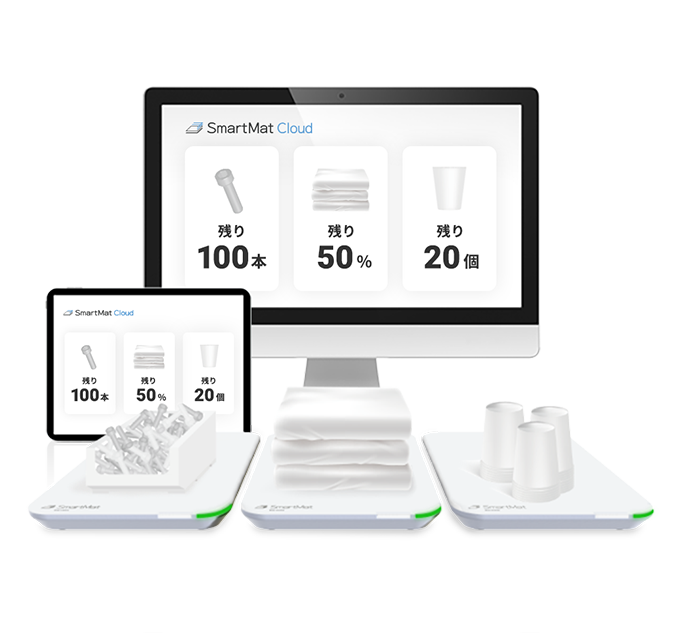
現場のあらゆるモノをIoTで見える化し、発注を自動化するDXソリューション「スマートマットクラウド」を使えば、簡単に自動化が可能です。スマートマットの上に管理したいモノを載せるだけで設置が完了。
あとはマットが自動でモノの在庫を検知、クラウド上でデータを管理し、適切なタイミングで自動発注してくれます。
さまざまな自動発注に対応
お客様の発注先に合わせた文面でメール・FAXの送信が可能です。
在庫圧縮を促進
推移を把握できるグラフで適切な在庫量を判断し、在庫圧縮を促進します。
置く場所を選びません
スマートマットはA3サイズ〜A6サイズまでの4サイズ展開。ケーブルレスで、冷蔵庫・冷凍庫利用も可能。
API・CSVでのシステム連携実績も多数
自社システムや他社システムと連携を行い、より在庫管理効率UPを実現します。
リアルタイム実在庫の見える化で生産工程のタクトタイムを適正化
スマートマットクラウドはリアルタイム実在庫の見える化で在庫管理、工程カイゼン・DXを進めるIoT SaaSプロダクトです。IoTで現場のモノの動きを捉え在庫管理を自動化、その上で工程内のモノの流れを分析し問題を見える化します。
さらにリアルタイム実在庫データを武器に工程を跨ぐ流れの澱みを特定しDX、現場力の向上に寄与します。
在庫置場に出向くことなくリアルタイムで管理画面から部品と仕掛品の在庫数を確認できます。在庫確認や補充タイミング把握のため、倉庫や工場内を走り回る必要はもうありません。
スマートマットクラウドは生産工程の進捗状況も可視化。後工程からひとつ前の工程に、必要な部品を、必要なタイミングで、いくつ必要かを自動で伝えることで、製造業の生産プロセスに潜むさまざまな課題を解消します。
AI x IoTで在庫最適化をし続けられる
スマートマットは、最新データ(入出庫の理論値ではなく、現場の実数データ)を溜め続けます。
そして、その大量データをAIが監視・解釈・検知。問題をタイムリーに抽出して改善を提案するので、常に在庫の最適化をし続けることができます。
◆特徴
- 遠隔で在庫を一元管理:倉庫や各拠点の在庫を管理画面で一元管理
- 需要に見合った供給を実現:ひとつ前の工程に伝え、過不足なく生産できる
- 生産効率を最大化:リアルタイムかつ自動で伝え、ムダがない