確認が取りづらい出庫もリアルタイムで把握
出庫を正確に管理し、ラインサイドへの供給を停滞させない
出庫を正確に管理し、ラインサイドへの供給を停滞させない

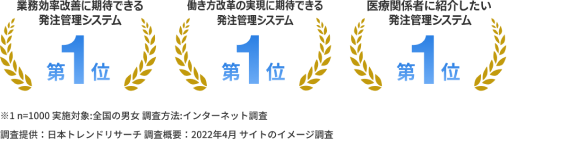
出庫のリアルタイム把握についての資料はこちら
3分でわかる資料をもらうこんなお悩み
ありませんか?
-
01出庫状況が確認しにくい管理形態や生産計画のズレによる予測不可な消費ペース出庫数や消費ペースを自動検知し在庫管理。さらに適切な量を自動発注
管理したいモノの下にマットを置くだけ。倉庫と各現場に置かれたIoT重量計で工場内すべての在庫量をクラウドから一元管理し、過剰在庫を排除。生産計画のズレにも左右されず、自動発注により常に適正在庫を維持
-
02原料の出庫間違いによる生産品の品質異常。廃棄・リカバリー生産のリスク管理したいモノと正しく紐づけられたIoT重量計により、出庫間違いを早期発見
IoT重量計のリアルタイム実在庫データを武器に不必要な出庫を早期発見。製造工程の投入前に検知して、不用品の廃棄やリカバリー生産を回避。
-
- リアルタイム実在庫データにより、ラインサイドへ効率的な供給が実現
倉庫だけでなくラインサイドの資材置き場にマットを設置すれば、適切なタイミングで必要な補充数量を倉庫担当者へアラートを発信。ラインサイドへのスムーズな供給が可能に
出庫状況の把握が難しい管理形態の改善に
成功した企業
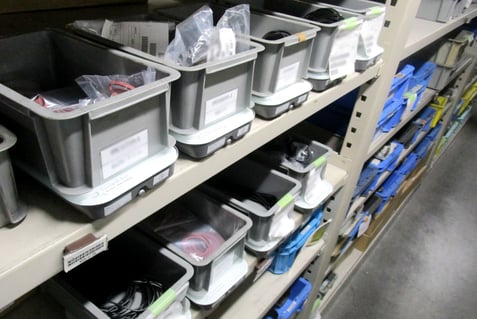
品薄に気づきにくい部品を出庫から的確に管理。適正在庫の維持に貢献
株式会社日立産機システム
導入目的
- 出庫状況を管理できず、品薄に気が付いてからの発注アクション
- 発注の業務工数が多く、欠品に至り生産ラインへの影響も
- 6000点以上の部品の在庫管理。月次棚卸はやむを得ず範囲を決めた循環棚卸
結果
- 出庫状況を把握でき、適正在庫の維持に貢献
- 発注の自動化で発注工数が激減し、機会損失をも抑制
- 月次の棚卸範囲が拡がり、棚卸自体も省力化