在庫管理術
7つのムダ【トヨタ生産方式に学ぶ在庫管理・工程管理のムダ取り事例】
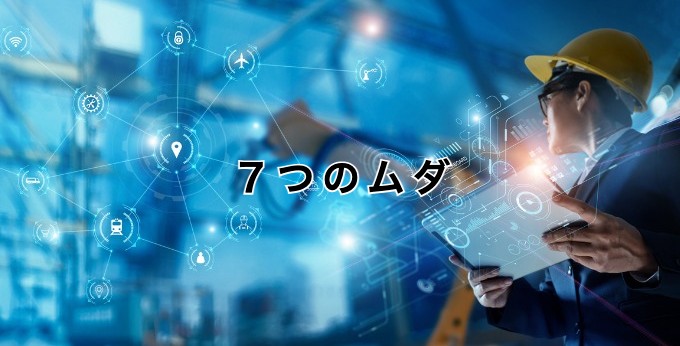
トヨタ生産方式の2本柱、「Just in time」と「ニンベンのある自働化」を支える4要素のうち、本記事では「7つのムダ取り」について分かりやすく解説していきます。
また、構内サプライチェーンを健全化するIoT重量計を用いた最新のソリューションで、どのようなムダとりが可能かを改善案や事例をご紹介。ぜひ最後までご一読ください。
\耳から学ぶ👂ポッドキャスト/
🎵音が流れます
7つのムダとは?【意味・歴史】
トヨタ生産方式の基本思想となる2つの柱が「ジャストインタイム(JIT)」と「ニンベンのある自働化」です。このトヨタ生産方式を実現するために4つの手法が用いられています。
4つの手法とは、カイゼン・問題の見える化・なぜなぜ分析・7つのムダ取りの4つ。今回はその中の「7つのムダ」についてトヨタのムダ取りの考え方とムダ取りの改善方法を事例を紹介しながら詳しく説明します。
記事後半では弊社のスマートマットクラウドを用いれば、どのようにムダを排除できるかの事例をいくつかご紹介。製造ラインや資材・商品の在庫のムダについて悩まれてる方はぜひご一読ください。
さらに、製造業における7つのムダに類似した3M(ムリ・ムラ・ムダ)についての記事も公開中です!
まずトヨタの生産方式とは?JITと自働化について
トヨタ生産方式のルーツは初代社長、豊田佐吉に端を発し、第二次世界大戦前後に2代目社長、豊田喜一郎氏がアメリカの自動車産業におけるライン製造方式をもとに組織だてていった歴史があります。
当時、熟練工が徴兵され生産力が低下したという背景があります。しかしそれからも長い年月をかけて改善を積み重ねたトヨタ生産方式は、今や世界中の製造業で注目・研究されている生産方式です。
多くの製造業が在庫を抱え、それを販売することで利益を得るという生産方式を採っています。しかしトヨタはあらゆるムダを徹底的に排除し在庫を抱えずに、「注文いただいた車を最も短い時間で効率的に作る」という目的の下、各工程が必要な時に必要なものだけ滞りなく生産するJIT方式を確立しています。
またニンベンのある自働化とは人の手が加わった自動化という意味です。「異常が発生したら機械を直ちに停止し、不良品を作らない」という考え方で、機械を止めて担当者が異常の原因を究明します。
生産の最も大きなムダである「不良品の排除」を目的とした仕組みであり、また徹底した原因究明はカイゼン・品質向上にも繋がります。
7つのムダの内容と改善
トヨタ生産方式では、製造現場のムダを以下のように分類しています。
- 加工のムダ
- 在庫のムダ
- 造りすぎのムダ
- 手持ちのムダ
- 動作のムダ
- 運搬のムダ
- 不良、手直しのムダ
加工のムダと改善事例
加工のムダとは製造工程から検査工程までの間に、本来は不要であるムダな作業が当てはまります。
製造基準や品質管理標準が適切に定まっていない場合や、もしくは「以前からやっていた」「念のためやっておきたい」といった経験的・心理的な理由で引き起こされる場合があります。
加工のムダの改善には本当に必要な作業かどうか、製品が必要な価値を得るために最小限の加工・検査になっているかを常に意識し、確認し続ける体制が必要です。
例えば以前に不良品が出て再発防止策を講じたにも関わらず、現場が自主的に検査作業をしている場合があります。その検査で実際に不良品の発生が防げているのか、検査履歴などを確認し必要のない検査であれば排除しなければなりません。
在庫のムダと改善事例
「急な発注が入った時のために」、「不良品を出した時のリカバリー用に」と在庫の理由が心理的なもので、現実的には不必要な資材を在庫で抱えること。
不必要な資材を在庫することで、保管場所が塞がったり、資材の管理・移動にも人件費がかかります。最悪の場合、資材が経年劣化して廃棄処分という結果にも繋がりかねません。
在庫のムダの改善には、顧客から発注・納品までの期間に生産リードタイムを合わせるというのが最も適切な改善方法です。
製造現場の努力としては加工のムダをなるべく減らし、リードタイムを縮小すること。
指示系統の努力としては在庫日数が最短にできるような生産計画を立てることであり、また営業努力としては生産計画に余裕がなければ納期を伸ばしてもらう、余裕があればなるべく早く納品させてもらう、といった納期調整により在庫のムダを軽減できます。
造り過ぎのムダと改善事例
7つのムダの中で最も低レベルなムダなのが「造りすぎのムダ」。指示系統や管理面が甘いと、必要な分ではなく材料がある分だけ製造してしまう場合があります。また、「いずれ必要になるだろう」と見切り発車的に製造してしまうことも。
商品や仕掛品の造りすぎは在庫のムダ・動作のムダ・運搬のムダ・材料の浪費のムダにも繋がります。現場とタクトの相互認識が合っていない・担当工程以外の進捗や在庫数が現場では見えにくいなどが原因と考えられます。
造りすぎのムダを排除するには、まず生産計画の見直し・現場との計画の徹底共有が必要です。生産計画は中・長期的な展望を持つのも大切ですが、現場や指示系統レベルでは1週間ごとに生産計画を見直す方が造りすぎのムダが防ぎやすいと言われています。
受注サイクルが安定している商品なら、それに生産計画を立てるサイクルを合わせましょう。例えば1週間に50個の製品を受注する場合、1ヵ月に1度200〜250個作るのではなく、1週間ごとに50個作る生産計画を立てるのがベスト。
一度に大量生産した方が製造工程の段取りが1回で済むのでムダがないように見えますが、在庫のムダに繋がります。受注サイクルが不安定な商品はどうしても在庫を持ってしまいがちなので、大量在庫はそういった商品を圧迫することになりかねません。
また予期せぬ受注が単発であった場合、生産計画のサイクルが短い方が新たに計画を立てやすいというメリットがあり、受注を取りこぼすということも軽減できるでしょう。
何よりも、こういった生産計画の背景や内容を現場と徹底して共有することで、造りすぎのムダを防ぐことができます。
手待ちのムダと改善事例
手待ちのムダとは、工員が手待ち無沙汰で作業することがない状態を指します。何も生み出さないのに人件費だけが発生します。
指示系統や生産計画・管理の甘さにより引き起こされがちなムダですが、原材料の配送遅延や前工程の遅延・機械トラブルによる作業ストップなども原因となります。また残念ながら工員が作業スピードを調整することで手待ちを隠すことも可能です。
手待ちのムダを防ぐには、まずは生産計画・管理を工場長から現場の班長まで同じ共通認識を持つことで、指示系統を統一することができます。
さらに工程ごとの作業進捗を把握できるような工夫や、配送遅延の場合はシステム点検や機械メンテナンス・クリーン度保持作業などを計画の中に柔軟に組み込めればよいでしょう。
また工員がスピードを調整し手待ちを隠す場合には、製品ごとの標準作業時間をしっかり割り出し、手待ちの有無を明らかにすることが必要です。
動作のムダと改善事例
動作のムダとは作業員の作業の習熟度合いによって生まれる、付加価値のないムダです。モノをひとつ落としただけでも、しゃがむ・探す・拾う・持ち替えるといったムダな動きが出てきます。
また動作のムダは現場が整理整頓できていない場合にも発生しやすく、ペンチや軍手・六角といった副資材や標準書ファイルなどがどこにあるか分からず、「探す」という動きも付加価値のない動作です。
動作のムダの改善事例としては、作業員の習熟度合いに応じて必要な研修を定期的に行う、また現場を整理整頓し、表示・保管場所を工夫して、ひと目でどこに何があるのか把握できるようにするなどが挙げられます。
運搬のムダと改善事例
現場への材料の搬入から後工程や検査工程への運搬、商品の出荷まで必要不可欠なのが運搬です。しかし何らかの価値を生み出すものではありません。
工程間の各現場や検査場までに距離があり、フォークリフトなどによる移動に時間や手間がかかる場合運搬のムダと言えるでしょう。
運搬のムダは工程・検査・最終出荷までの導線をなるべく短く、適切にすることで改善できます。
例えば複数工程の場合は、工程間の作業が順序よくいくように生産計画を立てる必要があります。前工程が終了したのに後工程が別の商品を製造していて、仕掛品を一旦、倉庫に保管しなくてはいけないという運搬のムダがないようにしましょう。
工程間で商品を梱包する場合もあり、これが過剰梱包になっていないか見直すことで運搬に関わる時間や動作のムダを排除できます。また運搬のムダに直結する造りすぎのムダも即座に排除すべきです。
ただし、工程ごとの建屋がどうしても離れている・消防法などである程度の空地が必要である・後工程の原材料の納品が遅れて生産計画がズレるなどの理由で、7つのムダの中で最も改善しにくいムダ。
不良、手直しのムダと改善事例
不良、手直しのムダは7つのムダの中で最も損失の大きいムダです。機械の条件設定ミスや装置の取り付けミスなどの見落とし、原材料や配合料の間違いといったヒューマンエラーが原因の多くを占めます。損失も大きいですがゼロにするのも難しいムダです。
不良品が発生した場合、製造ラインの停止・不良品の識別、回収など現場における人件費のムダを引き起こします。さらに不良品の廃棄にも原材料のムダや廃棄コストが内包されてることを忘れてはいけません。
また、不良品が発生した原因究明や再発防止策を講じるために、現場や製造管理の人間だけでなく技術本部の人間を呼ぶ必要があれば人件費だけでも大きな損失です。
さらにリカバリー(手直し、作り直し)をする場合、新たな材料・加工時間が必要となり、これも大きなムダと言えます。
製造品が1工程か複数工程か、また複数工程でも不良が発生したタイミングがどこかで損失度合いは変わりますが、最悪なのは納品してから顧客先で不良が発覚した場合です。この場合は営業も巻き込んでの手直しや再発防止策に務めなくてはなりません。は
不良品を造らないことが最善ですが、不良品をゼロにするのは非常に困難です。そのため製品に異常が出ればいかに早い段階で製造を止めるかが不良、手直しの改善となります。
基本的には製造標準書を遵守した生産を行い、品質検査装置を製造ラインに装着し異常を検知できるようにすれば即座に不良品を把握できます。異常を把握すれば製造ラインを停止、現場で被害を最小限に食い止めることが最も効率のよいムダの排除となります。
製造ラインを止めることは工場の稼働率の低下にも繋がるため、躊躇する現場の心理も働きますが、不良品を最小限に食い止めることは、原材料のムダ・不良品を破棄するムダを防ぎ、時間を置かずに異常を分析できるというメリットがあります。
7つのムダ取りに限界を感じているなら、「スマートマットクラウド」で現場に潜むムダを排除
「スマートマットクラウド」は原材料・仕掛品・製品・副資材まで、現場に存在するあらゆるモノの在庫をIoT重量計(スマートマット)で自動計測し、リアルタイムで実在庫を見える化。在庫量減少をリアルタイムで計測し、自動で発注管理ができるクラウド型在庫管理サービスです。
スマートマットの上に管理したいモノを載せるだけで、重量から算出された在庫数がリアルタイムで管理画面に反映されます。さらに、設定した閾値を下回ると、自動で発注や発注アラートをかける仕組みも構築。手動発注にも対応しており、業務スタイルに応じた柔軟な運用が可能です。
これらの機能により現場の在庫管理・発注関連業務を大幅に削減します。
リアルタイムなクラウド連携。「在庫のムダ」「手待ちのムダ」を排除
在庫量はすべてクラウド上で可視化されるので、視覚的に判断しやすい管理画面により、不動在庫や在庫の過不足をいち早く発見。在庫量が時系列で表示されるため、在庫圧縮に寄与し、「在庫のムダ」を省きます。
また、現場にわざわざ足を運ばなくても在庫状況の把握が可能。実地棚卸の労力を大幅に削減し、生産や出荷のタイミングを最適化できるため、「手待ちのムダ」を削減できます。
さらに、いつでもどこからでもログインできる管理画面を活用すれば、出荷・入荷・入庫・棚卸の作業もカンタン。入出庫履歴に担当者・メモの入力機能があるため、情報の属人化防止にも寄与します。
副資材の在庫管理にも活躍!「手待ちのムダ」「動作のムダ」を排除
原材料となる資材だけでなく、ベアリングやパッキン、メンテナンス用品や安全衛生用品など、管理が煩雑になりがちな副資材。スマートマットクラウドなら、部署ごと・生産ラインごと・建屋ごとなどにマットを配置すれば、管理画面から"どこに・何が・どれだけあるか"を即時に検索できるため、探し回る時間を最小限にできます。
「どこに何があるか分からない」「使いたいときに在庫がない」といった事態を防ぎ、探す・取りに行くといった非効率な「動作のムダ」を削減します。またこういった「動作のムダ」が生み出すチョコ停など、生産の「手待ちのムダ」を削減可能です。
副資材管理の効率化で、在庫と業務のムダを一掃
スマートマットクラウドは、現在多くの企業様に導入いただいています。スマートマットクラウドの自動発注で副資材管理を簡潔にすることで、在庫管理のムダを減らした事例をご紹介します。