在庫管理術
RFIDシステム|在庫管理や工程管理での活用術徹底ガイド
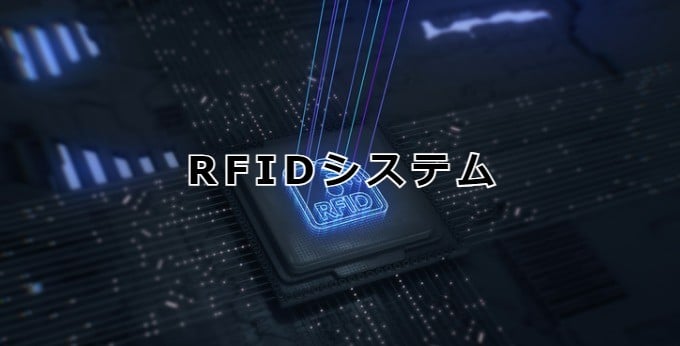
製造業や物流業界では、在庫や工程の「見える化」が求められています。RFIDシステムは、現場のデータをリアルタイムで収集し、経営判断に活かすための強力なツール、つまり現場と経営をつなぐ「可視化ツール」です。
本記事では、RFIDシステムの構成要素から、在庫管理・工程管理への活用方法、他システムとの連携による最適化までを詳しく解説します。
RFIDシステムとは?構成要素と基本の仕組み
RFID(Radio Frequency Identification)システムは、以下の3つの要素で構成されます。
- RFIDタグ※1
物品に取り付けられ、固有のIDや情報を保持する - リーダーライター
RFIDタグから情報を読み取り、必要に応じて書き込みを行う - 上位システム
収集したデータを管理・分析し、他の業務システムと連携する
これらの要素が同期することで、非接触・一括読取・リアルタイム追跡が可能となり、在庫や工程の可視化が実現します。RFIDシステムは在庫管理や物品貸出管理、製造業の工程管理に用いられています。
※1:二次元コードとは異なり、電波や電磁波を発している小型の「機械」。ICタグと呼ばれることもある。
関連記事:「RFIDとは」>>
在庫管理におけるRFIDシステムの実用例
RFIDシステムが在庫管理にもたらすメリットとは
RFIDシステムは、在庫管理において以下のようなメリットを提供します。
- 非接触・一括読み取り
複数タグを同時に読み取れるため、棚卸・入出庫作業の効率が向上 - 通信距離を担保する電波強度
高所や遮蔽されている場所にあるタグの読み取りも可能 - リアルタイム在庫把握
在庫の入出庫情報を即座に反映し、在庫状況を正確に把握 - トレーサビリティの向上
物品の移動履歴を追跡し、所在不明や紛失のリスクを低減 - RFIDタグは高寿命・高い汎用性
耐熱・耐久性・耐汚染はコード系より優れ、データの書き換え・追加が可能
近年では耐水性に優れ、200回までのクリーニングが可能なRFIDタグ※2があり、ユニフォームの貸出管理やホテル業界のリネン類の在庫管理に活用されています。
またデータを上書きできる特性から、たとえば店舗であれば検品・出荷・店舗保管・棚だし・販売済みなどの各状況を追加記録ができるため、物品のトレーサビリティとともにリアルタイムな状況把握に役立ちます。
※2:富士通フロンテックの技術。RFIDタグは水に濡れた状態だと読み取れないので、クリーニング完了後、乾いた状態のリネン類を読み込む。
RFIDシステムによる在庫管理の注意点や限界
RFIDは強力な在庫認識手段ではあるものの、導入や運用にあたり、いくつかの注意点や限界があります。
- 在庫形状によっては数量把握は不向き
RFIDは「1タグ=1物品」として認識するため、“重さ”や“容量”による数量変動の検出不可。消耗品や液体・粉体など、量で管理したい物品には不向きです。 - 読み取り環境の影響を受ける
金属や液体の近くでは、電波干渉によって読み取り精度が低下する可能性も。狭所や密集配置ではタグが重なり、誤読・未読が発生することもあります。 - 運用工数・コスト負荷
物品へのタグ貼付作業や、リーダー設置の物理的制約、タグ・機器のコストなど、導入初期にかかる手間と費用も無視できません。
RFIDタグを貼りつけられるモノには限界があります。使い捨ての消耗品(注射針やカテーテル)や小さな部材(ネジ・ナット)など、RFIDタグによる数量管理は難しいでしょう。さらに液体・粉体・コード状のものの残量や容量管理には不向きです。
さらに在庫ひとつ一つにタグ貼りの労力が発生し、一括読み取りが可能とはいえ、わざわざ現場に行きリーダーで読み取る工数があります。また高価※3なRFIDタグを使えばその分、ランニングコストは高くなります。リーダーはハンディや固定型で20万円、ゲート型で数万円など、初期費用がかかります。
これらの点を踏まえ、数量把握や連続モニタリングが求められる現場では、IoT重量計など別手段との組み合わせによる補完が有効です。
※3:RFIDの特許はアメリカが持っているので特許使用料として最低、1.5円はかかります。2023年現在のRFIDタグの最低価格は2〜3円ですが、読取精度の安定性や耐環境性に優れているRFIDタグであればより高価になってきます。
関連記事>>「RFID×在庫管理」
工程管理におけるRFIDシステム活用の広がり
工程管理におけるRFIDシステムのメリットと活用例
RFIDシステムは、在庫管理にとどまらず、製造業の各工程における可視化・進捗管理にも有効です。製造ラインや検査、梱包などの工程で物品ごとにタグを読み取ることで、進捗状況をリアルタイムに把握。工程ごとの作業時間や遅延発生箇所を「見える化」できます。
また、仕掛品のトレーサビリティ向上により「どこで滞留しているのか」をリアルタイムで把握できるため、リードタイム短縮や進捗遅延の未然防止にもつながります。
【具体的な活用例】
- アパレル業界
商品タグに各工程の処理履歴を追記することで、検品→出荷→店舗→販売までの流れを一括管理。返品対応や在庫ロスの削減にも効果を発揮。 - 自動車・部品製造業
各部品にタグを付与し、塗装・組立・検査といった工程の滞留状況や生産リードタイムの可視化を実現。生産性のボトルネック特定にも有効です。
自動車業界では20年も前から、車のボディの生産工程・搬送システムにおける生産フェーズ・履歴や生産指示の記録媒体としてRFIDシステムが導入されています。良品に限らず不良品の廃棄や手直しなどの情報も記録されます。
RFIDシステムによる工程管理の注意点や限界
工程管理でのRFID活用にも、導入にあたっての制約や注意点があります。
- タグの再利用性や破損リスク
複数工程を経る中で、タグが汚れたり破損したりする可能性があるため、物理的な耐久性や使い捨て前提の設計が必要です。 - 作業者スキャン忘れや環境エラー
手作業でタグを読み取る場面では、スキャン漏れ・読み取りミスがトラッキング漏れの原因になります。設備連携やゲート方式の併用が望ましいです。 - 工程間連携のシステム構築が必須
RFID単体では「履歴」は残せても、「分析」や「判断」はできません。工程の制御や見える化には、MES・ERPとのシステム統合が必要です。
耐久性の高いRFIDタグを使えば、ある程度はタグの再利用性は高まりますが、どうしても限界があります。また、耐金属・液体対応※4・読取精度の高いタグは一定の環境エラーを抑制しますが、そこに人手が加わるとどうしても人的ミスが発生します。
そこで導入効果を最大化するには、単なる導入に留まらず、業務フローやシステム設計の再構築といった、運用設計力も重要な要素となります。
※4:金属対応のものはUHF帯・HF帯に対応するものがそれぞれある。液体対応のものはUHF帯のモノが多い。また他にも180℃〜250℃の耐熱性に優れたものや、紫外線や溶剤に強い耐環境性に優れたRFIDタグがある。
RFIDシステム導入の課題と対処法
RFIDシステムは高機能でありながら、導入にあたってはいくつかの壁も存在します。環境や運用フローに適した設計と対処が不可欠です。
課題 | 内容 | 対処法 |
---|---|---|
金属・水の影響 | 電波が干渉を受けやすく、読み取り精度が低下 | 金属対応・耐環境型のタグを選定し、設置位置を工夫 |
タグ装着の手間 | 物品ごとにタグを貼り付ける工数が発生 | 自動タグ貼付装置や専用コンテナの活用で省力化 |
初期・運用コスト | タグやリーダー機器、保守費用がかかる | 段階的な導入とROI(投資対効果)を見据えた設計 |
上記のように、タグの選定やリーダー配置、上位システムとの接続方法など、現場環境に最適化したシステム設計が導入成功のカギを握ります。
特に工場や倉庫のような電波が届きにくい場所では、パイロット導入での精度検証や、限定エリアからのスモールスタートが有効。過剰投資を避けつつ、現場ニーズに即した最適構成を見出すことが重要です。
RFID × 他手段(IoT重量計など)で課題を補えるか
RFIDは履歴・識別に優れ、「誰が・いつ・どこで・何を」行ったかを記録・追跡することに特化した技術です。しかし、すべての在庫・工程に万能ではなく、苦手分野も存在します。
◆ RFIDの得意なこと
- モノの履歴や位置の可視化(トレーサビリティ)
- 特定人物や作業者とのひもづけ管理
- 工程の進捗ステー記録
◆ RFIDの苦手なこと
- 数量・残量の変動把握(タグ=個数でしか扱えない)
- 小型部品や液体・粉体など、タグ装着が難しい対象への対応
- 常時モニタリングや自動更新が必要な業務には不向き
RFIDの課題を補完する手段として、IoT重量計やAIカメラが注目されています。特にIoT重量センサは重さにより、管理したいモノの数量の自動計測が可能。RFIDシステムのように1タグ=1個ではないため、消耗品や液体の残量・容量管理もできます。
さらに24時間365日モニタリングができる高性能なIoT重量計であれば、在庫管理だけではなく、生産ラインを含む工場サプライチェーン全体を常時監視できる手段としても有効です。
RFIDシステムの課題をスマートマットクラウド(IoT重量センサ活用)がどう補完するか
スマートマットクラウドとはIoT重量センサ(スマートマット)を用いて、24時間365日、リアルタイムでモノの推移を可視化するクラウド型システムです。在庫管理に限らず、生産ライン周辺の補充効率化や仕掛品推移の可視化など、生産工程の管理・監視にも適しています。
◆ スマートマットクラウドができること
- モノを“載せるだけ”※5で数量や残量/割合をリアルタイムで自動計測
- 発注点を下回った際には自動アラートを発報
- 小さな部品や液体・粉体のようなタグが貼れない物品にも対応可能
両者の特性を踏まえると、RFIDシステムとスマートマットクラウドを連携させたハイブリット運用によって、以下のような効果が期待できます。
※5:重量センサ(スマートマット)のシリアルNoと積載物を管理画面上で紐づければOK
領域 | RFID | スマートマットクラウド |
---|---|---|
履歴管理 | ◎ 履歴・識別に強み | △ 連携で補完 |
数量・残量の把握 | △ 個体カウントのみ | ◎ リアルタイムに自動計測 |
対象物の柔軟性 | △ タグ貼付必須 | ◎ タグ不要・多様な物品に対応 |
工程連携 | ◎ MES・BOMと連携可能 | ◯ 在庫→工程連携が可能 |
RFIDの「履歴・識別」とスマートマットの「数量・状態把握」を組み合わせることで、現場の“動き”と“量”を多面的に可視化する統合管理の実現が期待されます。
ハイブリット運用|SmartOP(RFID)× SmartMat Cloud(IoT重量計)
SmartOPとはRFID簡易システムであり、スマートマットクラウドと連携することで、工程進捗と在庫量を一元で“見える化”します。
- RFIDタグでモノの個体識別を把握
- スマートマットでモノの数量・残量を自動計測
- API連携により、両者のデータを統合ダッシュボードに集約
これにより以下のような現場課題に対して、デジタルでの解決が可能となります。
「タグが貼れない」「スキャンの手間がある」「工程ごとに可視化ができていない」といった制約に悩む現場では、RFIDとスマートマットクラウドの連携によるハイブリッドな可視化と最適化が大きな武器になります。
また例えば、工程管理で作業履歴を記録できるRFIDタグを活用すれば、どのような工程を辿ってきたか・次に何をすべきかという判断材料が与えられます。そのため、近年ではかんばん方式・BOMのシステム統合などでRFIDタグを活用する動きが見られます。
しかし、RFIDタグには、資材が不足しそうな状態や仕掛品が滞留・欠品している状態をリアルタイムで把握し難いという弱点があります。そういった点では、正確に数量を自動計測するIoT重量計が活躍します。
仕掛品・中間品をIoT重量計に載せることで、工程間の進捗のズレや澱みをリアルタイムで把握することが可能※6。工程間のモノや情報の整流化に役立ちます。
※6:重量センサ同士を連携させてリアルタイムなモノの流れをデータとして取得、記録。管理部門や各工程に設置したモニターでデータを閲覧でき、工程ごとの進捗をコミュニケーションコストをかけることなく把握可能。
IoT重量計を用いたスマートマットクラウドの基本性能
在庫最適化AIエージェントにより、"在庫を最適化し続ける"
株式会社エスマットが2025年6月に新たにリリースした生成AI「在庫最適化AIエージェント」により、在庫の最適化を自動的に実行できる仕組みが実現しています。
この生成AIは、IoT重量計によるリアルタイムな在庫情報を基に、AIが需要傾向を学習・予測。現場に即した発注タイミングや適正在庫数を提案し、人手による判断の属人化や遅れを最小化します。
さまざまな自動発注に対応
お客様の発注先に合わせた文面でメール・FAXの送信が可能です。また一日複数回の高回転発注や発注残を考慮した高度な発注システムを実装しています。
置くモノ・場所を選びません
スマートマットはサイズ展開が豊富かつ複数枚使用(マルチマット)が可能で、さまざまな重さ・形状の在庫に対応できます。ケーブルレスで、小さなラックや引き出しのなか、冷蔵庫・冷凍庫利用も可能。
API・CSVでのシステム連携実績も多数
自社システムや他社システムと連携を行い、より業務効率UPを実現します。簡易RFIDシステム:SmaOpへの連携も可能で、実績も多数。ハイブリット運用体制を整える支援も行います。
棚卸差異を解消したスマートマットクラウド導入事例
スマートマットクラウドは、現在多くの企業様に導入いただいています。重量センサによる管理で在庫管理の効率化に成功した事例をご紹介します。