在庫管理術
リーン生産方式【トヨタ生産方式との違いやメリット・デメリットは?事例も交えてご紹介】
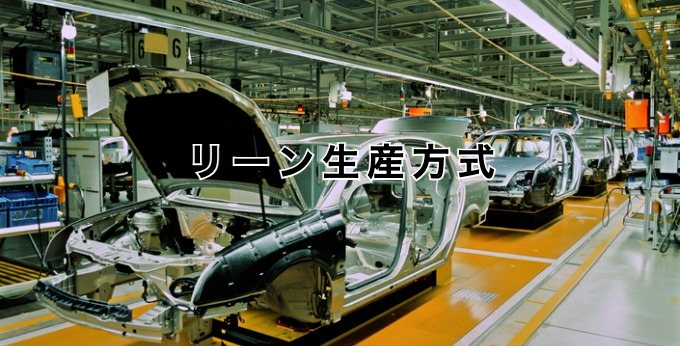
本記事では、リーン生産方式について定義やメリット・デメリットを分かりやすく解説していきます。
また、化学系機能材工場にリーン生産方式を導入した際の具体的な改善の流れやムダ取りに役立つ最新IoT機器をご紹介。ぜひ最後までご一読ください。
リーン生産方式とは?
リーン生産方式とはアメリカのマサチューセッツ工科大学のジェームズ・ウォマックが紹介した生産方式で、leanには「贅肉が取れて引き締まった状態」という意味があります。つまり、ムダを徹底的に排除したスマートな生産方式という意味合いとなります。
ただしリーン生産方式はウォマック教授がトヨタ生産方式を研究し、それを整えて体系化した後に、トヨタ固有の方式ではなく一般的にも通用する方式として紹介したもので、基本的な内容はトヨタ生産方式とほとんど同じです。
リーン生産方式とトヨタ生産方式の違い
トヨタ生産方式から生まれたリーン生産方式は、トヨタ生産方式と同じくジャスト・イン・タイムやニンベンのある自働化が基本思想です。
この2つの柱を支える3M(ムダ・ムラ・ムリ)や7つのムダ取りといった考え方に加え、なぜなぜ分析・問題の見える化・カイゼン*1・5Sや改善*2といった業務効率化における手法もよく研究されており、それらが整理され体系化されています。
トヨタ生産方式がトヨタの現場で数十年かけて試行錯誤を繰り返しながら体系化されたトヨタ固有の生産方式に対して、リーン生産方式は一般向けに体系化され、さまざまな製造業に提供されています。
またリーン生産方式は「トヨタ生産方式の別名」という程度に考えられている場合もありますが、海外では一般向けに体系化されていることいることから、トヨタ生産方式より有名です。
その背景には、工学部の取得科目になっていたり、リーン生産方式専門のコンサル業があることにも起因しています。コンサルタントがある製造業にリーン生産方式を導入する場合は、予算や規模に合わせて導入内容をマッチさせ、さらにチェックリストや標準書など一式をパッケージ化して提供します。
※1,2「改善とカイゼンの違い」:改善とは悪い状況を良くすること。カイゼンとは悪い状況には陥っていないが、現状に満足せずより良い状況に変化させること。
リーン生産方式とかんばん方式
後工程が部品を引き取ったことをトリガーとし、無くなった分を前工程が作る「かんばん方式」は、JITを実現するひとつの手法としてトヨタがスーパーマーケットの棚出しをヒントに発案した生産方式です。
つまり後工程が必要な部品の発注を前工程に対して行い、この発注書が「仕掛けかんばん」となり、前工程がこの仕掛けかんばんに沿って生産し後工程に納品する際に、納品書が「引き取りかんばん」となってモノと一緒に後工程へ流れていきます。
必要な時に必要なモノだけという「JIT」という考え方には有効な生産方式であり、リーン生産方式にも採用されています。
ただし、かんばん方式は不良品が出ないことを前提とした考え方であり、前工程で不良品が出ると直ちに欠品に繋がるのがデメリットです。また多品種小ロット生産には不向きであるため、全ての製造業にマッチした方式ではありません。
リーン生産方式のメリット
リーン生産方式のメリットはトヨタ生産方式と同じく、生産工程の徹底した効率化・ムダの排除、またトラブルや不良品への迅速な対応を取りつつも、従来の生産工程と同等以上の価値を製品につけることが可能な点です。
さらに商品のようにパッケージ化されているリーン生産方式は、コンサルタントと相談しながら生産工程に導入できるため、トヨタ生産方式を直接まねるよりもはるかに自社の製造プロセスにマッチングしやすくなっています。
また海外の企業だけでなく日本国内の企業が工場を海外進出させる際に、コンサルタントに頼れる・海外の製造業界では一般的に知られた生産方式のため現地の人間にも納得してもらいやすい、というメリットがあります。
リーン生産方式のデメリット
リーン生産方式のデメリットは、「必要なモノを必要なときに必要な分だけ」というジャストインタイム(JIT)を基本理念としているため、生産工程で何らかのトラブルがあると問題解決力に乏しい現場の場合、すぐさま製品の欠品に繋がる点です。
複数工程の場合、最初の工程でトラブルが発生し早期解決できなければ、生産ライン全体が停止することにもなりかねません。さらに現場で不良品を見逃した場合、検品工程での発覚や最悪の場合、顧客先での不良品の発覚となり、大掛かりな不良・手直しのムダが発生する可能性があります。
またJITでは余剰在庫を持たないため、平均的な歩留まり*3を考慮し必要な資材を準備していたとしても、不良品やトラブルが繰り返されれば、資材在庫の欠品にも直結します。
そのため、現場の作業員の生産ラインや機械の扱いの習熟度、製品そのものへの理解度を深める必要があり、新人への研修期間だけでなく作業員全体にも定期的な研修や意識改善する工夫*4を行い、問題解決力を高めることが必要です。
さらに、資材や梱包材、運搬費用についても必要な分だけ手配するため、残念ながら大量発注によるコストダウンは期待できません。
*3:製造業では原料に対する完成品の割合を歩留まりという
*4:生産方式の基礎教育から改善やカイゼン1案件に対する手当や評価項目の導入など
リーン生産方式の事例
化学系機能材工場における製品Aの生産にリーン生産方式を導入した事例を紹介していきます。
現状調査から改善チームの設立
まずは既存の製品Aの生産工程における現状調査を行う。問題の見える化とムダの洗い出しから「モノと情報の導線」を作成する。
その上で現場の作業員の協力を得て、生産部隊とは別に改善チームを設立し各種改善*5を行った。
*5この場合、カタカナのカイゼンの意味も含む
●工場の現状調査 ●製品A:フィルム製品 |
製品Aの現状調査・モノと情報の導線
|
ムダの洗い出し・改善活動・是正処置
●改善活動①
現状調査①に対して、運搬・生産計画のスムーズ化のために全ての工程を2 、3工程の生産ラインで行えないか検討する。4M変動にも関わることなので顧客先とも連携し全工程の試作を2、3工程の生産ラインで行った。
結果:機械差による決定的な外観の違いが発生した。1工程目の生産ライン変更はNG
●改善活動②
現状調査②に対して、過剰梱包ではないか検証を行った。
結果:工程間に日数またぎがある場合、倉庫に縦積みすることから側板を使用した宙吊り・箱入れ梱包は不可欠。また日数またぎがなくとも、建屋間の移動でホコリや虫の付着がコンタミに繋がるため箱入れは不可欠となった。
●改善活動③
現状調査③、④に対して運搬のムダではないか検証を行った。
結果1:実際に運搬のムダが発生していた。工程1→工程2、3をスムーズに行えるように生産計画を改善し、また各工程の進捗度合いを現場の班長レベルで確認できる工夫をして、運搬のムダを解消した。
さらに生産計画を1週間の短いサイクルで生産管理部隊が見直すことで、工程間の進捗のズレが減少した。
結果2:深夜や早朝に仕掛品の移動が必要な場合、工場の現場とそれ以外の勤務形態の違いにより、資材係のフォークリフト操縦者が出勤するまで待たなくてはいけないという手待ちのムダが発生していた。
そのため現場の各班の作業員の少なくとも1人にフォークリフトの免許を取らせ、仕掛品の搬入を直ちに行うことができるようにした。
●改善活動④
現状調査⑤、⑥について品質チェックが適正にかつ最小限に行われてるか確認した。
結果:1工程目の品質チェックは最小限となっており、これまで問題も発生していない。また2、3工程目は難易度が高く、生産ライン上の品質検査装置により幾度か異常の発見・即座のライン停止に繋がっており自働化に貢献されているため現状でOK。
●改善活動⑤
現状調査⑦について現場の各班で、ロールマップとは別に詳細な加工チェックリストが作成されていた。内容が多数、ロールマップと重複していた。
結果1:ロールマップについてモノ自体の状態のみ把握できる必要最小限の情報を記載する仕様に変更し、情報過多による書き込み・読み取りの動作のムダを排除した。
結果2:加工チェックリストはトラブルや品質異常が発生した際のなぜなぜ分析に役立つと判断し現状維持とした。
●改善活動⑥
現状調査⑧についてはJITの基本理念に則っているため、OKとした。
改善結果・ヨコ展開
製品Aでは生産計画の見直しと現場作業員のフォークリフト操縦を可能にしたことで、「運搬のムダ」を排除、また勤務形態の違いによる「手待ちのムダ」を排除した。
加工チェックリストとロールマップの重複のムダの排除も含み、結果的に製品Aでは生産リードタイムが35%削減された。フォークリフト操縦者には別途、就業内容の契約更新や操縦手当を実施。
またその他の商品でも、製品Aの改善結果のヨコ展開を実施した。生産計画は1週間の短いサイクルで毎回見直すことで、計画の乱れを最小限に抑えられた。そうすることで、現場作業員のフォークリフト操縦の必要性・負担を抑えつつも、運搬のムダ・手待ちのムダを軽減できるようになった。
各現場で保持している加工チェックリストと製品に記載されているロードマップの重複を全製品に渡り改善した。製品全般に対して重複書き込み・読み取りの動作のムダを排除することができた。
さらに全製品の資材・梱包材もJITに則り「必要な時に必要な分だけ」準備するようにした。全製品では対応できなかったが約80%の製品で対応可能となった。結果、工場全体ではリードタイムを約15%削減できた。
今回は、現場作業員にそもそも「品質異常がある際は直ちにラインを停止する」というニンベンのある自働化の基本概念があり、また管理側も含み工場全体で問題解決力が高かったので改善がスムーズに受け入れられた。問題解決力や意識の高さもリーン生産方式の導入の成功に大きく貢献している。
リーン生産方式のムダ取りに役立つ「スマートマットクラウド」
現場のあらゆるモノをIoTで見える化し、発注を自働化するDXソリューション「スマートマットクラウド」を使えば、在庫量やモノの流れが可視化でき、管理の難しい仕掛品も正確にカウントします。
重量測定のため、スマートマットの上に管理したいモノを載せるだけでリアルタイム計測。あとはマットが自動でモノの在庫を送信し、クラウド上でデータを記録し管理。適切なタイミングで自動発注してくれます。
置くだけで在庫量を可視化でき「在庫のムダ」を排除
倉庫や各拠点の点在している在庫、冷蔵庫やラックの中など、見えない場所の在庫も遠隔から一元管理します。
在庫一覧表や在庫推移グラフで在庫量がひと目で分かるので、過剰在庫や滞留在庫の把握が可能。スマートマットクラウドで在庫のムダを排除できます。
アプリで入出庫管理すれば生産の段取りもスムーズに
スマートマットクラウドのアプリを使えば、手書きの入出庫伝票や使用状況のエクセル入力も不要!スマホアプリでカンタンに読み込み・クラウドにデータを転送します。
現場の作業員も資材管理係も、入出庫の際の事務作業が削減されることで生産の段取りがスムーズとなり、生産リードタイムの縮小に繋がります。
欠品・滞留在庫も早期解決!リアルタイム実在庫を把握
資材倉庫だけでなく、各現場の一時置き場のモノの管理にもマットを使えばリアルタイムで現場の在庫状況が可視化できます。
従来のかんばん方式では見えにくかった前工程の滞留在庫や後工程の欠品が、各現場・管理側で早期に把握しやすく、生産管理システムへの入力の手間やコミュニケーションコストをかけることなく、工程間の連携をスムーズにし生産リードタイムを短縮します。
AI x IoTで在庫最適化をし続けられる
スマートマットは、最新データ(入出庫の理論値ではなく、現場の実数データ)を溜め続けます。
そして、その大量データをAIが監視・解釈・検知。問題をタイムリーに抽出して改善を提案するので、常に在庫の最適化をし続けることができます。
◆特徴
- 遠隔で在庫を一元管理:倉庫や各拠点の在庫を管理画面で一元管理
- 需要に見合った供給を実現:ひとつ前の工程に伝え、過不足なく生産できる
- 生産効率を最大化:リアルタイムかつ自動で伝え、ムダがない
無駄を排除し、生産性向上につながったスマートマットクラウド導入事例
▼積水成型工業株式会社様のインタビュー動画はこちら