在庫管理術
【2025年最新】在庫管理改善DXガイド|欠品ゼロを実現する7ステップ
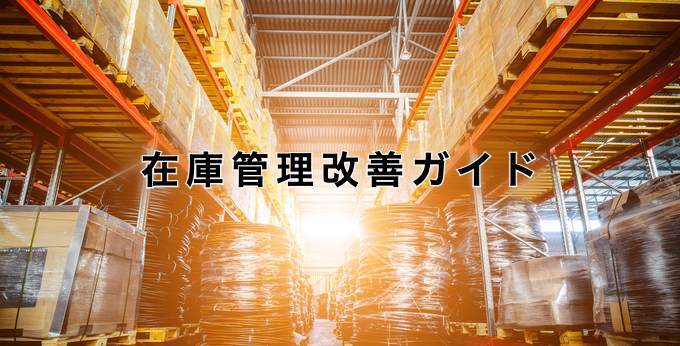
世界的な物流遅延と人手不足が長引く今、在庫管理は企業成長を左右する最優先課題です。本ガイドでは最新統計と実例を基に、現状を数値で把握し、DXツールで欠品ゼロ・過剰在庫削減をめざす 7 ステップを解説します。
導入ロードマップや補助金情報、読み終えた瞬間から使えるチェックリスト付きで、半年以内に ROI を可視化できる在庫管理改善の実践ノウハウを提供します。
今こそ在庫管理を改善すべき3つの理由
物流混乱・人手不足の加速
パンデミック後も続く国際物流の混乱とエネルギーコストの高止まりは、あらゆる業界の調達計画に大きな揺さぶりをかけています。経済産業省の調査によれば、2024年の主要製造業における平均リードタイムはコロナ前比で18%長期化※1し、出荷遅延による逸失売上は前年比12%増加しました。さらに国内の倉庫・物流現場では有効求人倍率が3.4倍※2(2025年1月時点)に達し、人材確保コストが急騰しています。
このような環境下で在庫管理の課題解決を怠っていると、キャッシュが滞留するだけでなく、欠品による販売機会損失が雪だるま式に拡大します。改善を急ぐべき根拠を次の3つの観点から整理します。
(※1) 経済産業省『2024年版ものづくり白書』第1部「製造業を取り巻く環境変化」より抜粋。
(※2) 厚生労働省『一般職業紹介状況(令和7年1月分)』産業別(倉庫・運輸関連)データ。
在庫管理の改善を急ぐべき3つの根拠
1.サプライチェーン混乱の長期化
・港湾混雑や輸送コスト高騰が続き、リードタイムは平均15〜20%延伸
2.人手不足による業務停滞
・倉庫スタッフの離職率は前年比12%増。棚卸や検品に割ける工数が慢性的に不足
3.機会損失と在庫コストの隠れ雪だるま
・欠品で逸失する粗利額、滞留在庫の保管・廃棄コストが利益を圧迫
これらの課題を解決する鍵は在庫管理の現状を数値で把握し、DX(デジタルトランスフォーメーション)で継続的に最適化する仕組みです。
ステップ1:在庫管理KPIを可視化する
ただDXツールを導入しても、基礎指標が計測できていなければ改善幅を検証できません。まず在庫管理KPIを設定しどこにムダやボトルネックがあるか数字で炙り出します。
ここでは3 つの最重要KPIと、計算を自動化するテンプレートの作り方」、さらにKPIをリアルタイムで可視化する方法を紹介します。
主要な在庫管理KPI と計算式
数字で現状を把握し、可視化→最適化→自動化へと段階的に在庫管理改善を進めます。
- 欠品率 = 欠品 SKU数 ÷ 全 SKU数 × 100(%)
- 在庫回転率 = 年間売上原価 ÷ 平均棚卸資産(円)
- 棚卸工数 = 棚卸作業時間(h) ÷ 棚卸回数
KPI可視化ツールを活用
表計算のシートとAppSheetをつなぐと、現場データがリアルタイムにダッシュボード化され、異常値を即検知できます。
- Google スプレッドシートに入力フォームを作成(SKU 数・売上原価・作業時間など)
- AppSheet でシートを読み込み、ノーコードでダッシュボードを生成
- グラフウィジェットに「欠品率/在庫回転率/棚卸工数」を配置し、モバイル表示を有効化
●ポイント
値の上限・下限を条件付き書式で色分けすると異常値がひと目で分かりやすくなります。
ステップ2:在庫管理改善ソリューションを選定する
在庫管理の改善を成功させるには「可視化→自動化→最適化」の3レイヤーをカバーするツールが必要です。現場データを集めるクラウドWMS、数量をリアルタイムで測定するスマートマットクラウド/RFID、需要変動を先読みするAI需要予測の概要を整理します。
クラウドWMS(倉庫管理システム)
- SaaS型:サーバーレス+月額課金でスモールスタート
- 主機能:入出庫・ロット/ロケーション別在庫・バーコード処理
- 費用感:月額3〜10万円+ユーザー課金
- 導入期間:最短2〜3か月(マスタ整備+テスト移行含む)
●ポイント
オンプレミスWMSからの移行は、まず "ハンディ運用→モバイル+API" への段階移行で現場負荷を軽減。
スマートマットクラウド/RFID
- スマートマットクラウド:IoTが在庫の重量を計測、読み取り作業なしで棚卸自動化
- RFID:一括読み取りで棚卸工数削減
●ポイント
連続計測が必要な毒劇物や金属部品、液体はスマートマット、 トレーサビリティ管理やロット管理が必要な資材はRFIDと役割分担を明確に。
AI需要予測
- 仕組み:過去販売・季節性・販促・外部指数を機械学習で重み付け
- 導入フロー:①CSVで需要データ投入→②ベースモデル学習→③PoC(2〜3か月)→④ERP連携
●ポイント
まずは ABC分析上位20%の品目で精度を検証し、ROIを可視化してから全SKU展開するとリスクを抑えられます。
ステップ3:在庫管理ソリューションを比較する
ソリューション | 費用 | 導入工数 | 拡張性 | サポート |
---|---|---|---|---|
クラウドWMS | ★★☆☆☆ | ★★☆☆☆ | ★★★★☆ | ★★★★☆ |
スマートマットクラウド | ★★★☆☆ | ★★★★☆ |
★★★★☆ |
★★★★☆ |
RFID | ★★☆☆☆ | ★★☆☆☆ | ★★★★☆ | ★★☆☆☆ |
AI需要予測 | ★★★★☆ | ★★★★☆ | ★★★★★ | ★☆☆☆☆ |
費用は月額+初期費用、導入工数は要件定義〜現場稼働までの目安。
ステップ4:KPI改善インパクトを試算する
在庫DXへの投資判断では、導入前に改善幅とROIを数値で予測することが不可欠です。本ステップでは、現状ベースラインの採り方とツール別ROIシートを使ったインパクト試算の手順を示します。
1. ベースラインを固める
- 欠品率/在庫回転率/棚卸工数など主要KPIを過去3か月平均で算出
- 季節変動が大きい業種は前年同月も併記
2. 改善インパクトを試算する(サンプル)
KPI | 現状 | 試算改善幅 | 目標値(6か月後) |
欠品率 | 4.8% | ▼3.0pt | 1.8% |
棚卸工数 | 60h/月 | ▲25h | 35h/月 |
在庫回転率 | 3.2回/年 | +1.0回 | 4.2回/年 |
ツールベンダーのROIテンプレートがあれば、活用。自社の販売・在庫・作業時間データを入力すると、自動でキャッシュ創出額と投資回収期間が算出されます。
ステップ5:導入ロードマップを作成・社内稟議を通す
在庫DXを成功させるには、導入プロセスを可視化し、稟議で数字と根拠を示すことが欠かせません。ここでは6か月で本番稼働を目指すロードマップと、承認を得るための稟議書ポイント、さらに活用できる補助金スケジュールをまとめます。
導入ロードマップ(6か月)
月 | 主なフェーズ | 具体タスク | ガントチャート指示 |
1 | 現状分析・KPI設定 | ・在庫データ収集・欠品率/棚卸工数を3か月平均で算出 | ─██────────── |
2 | PoC計画策定 | ・対象SKU/拠点を選定・ツール要件定義 | ──██───────── |
3 | PoC実施 | ・クラウドWMS初期設定・スマートマット/RFID設置 | ───██──────── |
4 | PoC評価・ギャップ分析 | ・KPI実測 vs 試算を比較・追加要件洗い出し | ─────██─────── |
5 | 本番環境構築 | ・マスタデータ移行・API連携テスト | ──────██────── |
6 | 教育・全社展開 | ・現場トレーニング・KPIダッシュボード公開 | ───────██───── |
ポイント
- 現場巻き込み:ベースライン測定を現場主導で行い、データの信頼度を高める。
- 小規模PoC:SKUを絞り、測定コストとリスクを最小化。試算と実測の差を早期に把握できる。
- KPI目標の先置き:数値コミットを宣言しておくと経営層の支援を得やすい。
社内稟議書の書き方
稟議書を作成する際は「目的・投資額・ROI・リスク・スケジュール」の5要素を示します。
-
目的・背景:物流混乱/人手不足→在庫可視化の必要性を定量データで記載
-
投資額・内訳:初期費用+月額+人件費削減見込み
-
ROI計算式:(キャッシュ創出額 − 総投資額) ÷ 総投資額 × 100%
-
リスク・対策:データ移行/現場定着/サイバーセキュリティ
-
スケジュール:「導入ロードマップ」を貼付し、マイルストーンを明示
社内稟議を通す3つのコツ
現場を巻き込んでベースライン計測を現場主導で実施すれば、データの信頼度が高まり、稟議段階での反対意見を未然に防げます。さらにSKUを絞った小規模PoCにすることで測定コストを抑えつつ、費用対効果を明確に示すことが可能です。また、KPI目標をあらかじめ数値でコミットしておけば、経営層から理解とサポートを得やすくなります。
【費用対効果に+α】社内稟議書に追加すべきポイント
目標値は絶対値:数値は財務指標へ変換し、意思決定者が一目で判断できる形に整えます。「現状比〇%改善」より「欠品率〇%以下」などで示すと社内合意が取りやすくなります。
-
機会損失を可視化:ツール未導入時に生じる欠品・緊急調達・滞留在庫による損失額を示し、導入遅延のリスクを経営層に明示します。
-
周辺工程コストも算入:棚卸・ピッキング・データ入力など在庫管理以外の作業時間と人件費削減効果を試算し、ROIを底上げすることを明言します
3つのシナリオを準備:不確実性を加味し、悲観・標準・楽観の3シナリオで提示すると説得力が増します。
ステップ6:補助金活用を活用する(2025年最新スケジュール)
在庫管理の改善にツール導入に補助金を活用し、初期投資を最小化できます。導入コストを最大1/2まで圧縮し、ROIを大幅に向上させることが可能です
●2025年補助金スケジュール補助金の一例 | 公募期間(予定※) | 採択率の上げ方 |
IT導入補助金(通常枠) | 受付開始:3/31〜 第1回締切:6/16 17:00 (※以降随時更新) |
・業務プロセス改善効果を数値で示す・デジタル投資+人材育成をセット申請する |
ものづくり補助金 | 受付開始:9/1〜 第1回締切:10/15 17:00(※予定) |
・革新性と市場性を明確化・補助事業終了後3年間の売上計画を添付 |
●補助金の採択率を高めるコツ
- PI改善幅を具体的な金額に換算します。
- 現場写真や業務フロー図を添付し、改善ビフォーアフターを視覚化します。
よくある失敗とリスク回避策Q&A
Q1. データ移行でトラブルが起きる理由は?
A. 旧システムのマスター不整合やSKUコード重複、桁数不一致が主因です。事前にデータクレンジングを行い、テスト環境で移行リハーサルを実施してリスクを最小化します。
●事前データクレンジング手順の例
- SKUマスターの正規化(コード統一・重複排除)
- 欠損値・異常値の洗い出しと補完
- 移行用CSVを生成し、検証環境でインポートテスト
- エラーログを分析して再クレンジング→本番移行
Q2. 現場がツールを使いこなせない場合は?
A. UIへの抵抗感や操作ミスが原因です。段階的なオンボーディング研修を行い、操作方法の定着率を高めます。
●オンボーディング研修プランの例
- キックオフ講習(90分):基本操作と業務フローをハンズオン形式で習得
- ローンチ直前リマインド(30分):FAQ共有+ミニクイズで理解度チェック
- ローンチ後フォロー(2週間):チャットQ&Aとショート動画マニュアルを配信
- 1か月後レビュー(60分):操作ログを基に改善点をフィードバック
まとめ:キャッシュを生む在庫管理へ。改善の最適な一手を。
半歩でも前に進める最短ルートは「まずデータを集め、KPIをグラフで確認する」ことです。今日からアクションを起こし、半年後には欠品ゼロ・過剰在庫削減を達成する在庫管理DXを現実のものにしましょう。
【7ステップ要点】
1. KPIを数値化する ── 現状を“見える化”して問題点を特定
2. 改善ツールを選定する ── 可視化・自動化・最適化の3層をカバー
3. 選定ツールを比較する ── 費用・導入工数・拡張性・サポートを★評価
4. 改善インパクトを試算する ── ROIを数値で提示し投資判断を加速
5. 導入計画と稟議を通す ── 6か月ロードマップと稟議書テンプレで合意形成
6. 補助金を活用する ── IT導入補助金・ものづくり補助金で初期投資を圧縮
7. よくある失敗を回避する ── データ移行・定着のリスクを事前対策
スマートマットクラウドで在庫DXを最短実現
IoT重量センサーとクラウドを融合した 「スマートマットクラウド」 は、在庫数量の自動計測から閾値発注、ダッシュボード可視化までをワンストップで提供します。在庫の管理の可視化・自動化・最適化を、1 つのプラットフォームで同時に実現できるのが最大の強みです。
マットの上に置きっぱなしで、モノの動きの可視化
目視・カウント不要で、データが見えて、意思決定がよりしやすくなります。
欠品も過剰も解消。在庫を最適化
在庫金額を設定すると、在庫金額の推移を自動でグラフ表示します
不動在庫の特定
在庫金額を設定すると、在庫の動きから過剰在庫リスクとなる「不動在庫」を把握できます。
在庫管理改善成功事例
伸和コントロールズ株式会社様の導入事例
-
導入前:理論在庫と実在庫の乖離が大きく、棚卸に60h/回。倉庫スペース逼迫。
-
導入後:棚卸工数を50%削減し、過剰在庫率を40%低減。棚卸時間 60h → 30h/月、在庫回転率も向上。