在庫管理術
理論在庫|理論在庫とは?実在庫と乖離しやすい理由と対策
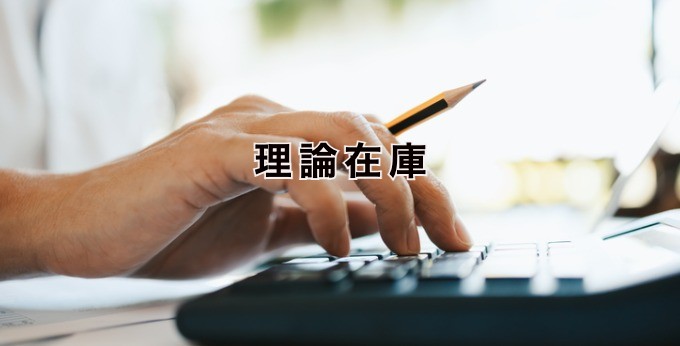
在庫管理では、「帳簿上では在庫があるはずなのに現場にない」「帳簿の数と現場にある在庫数が合わない」といった混乱が頻発します。
こうした事態を防ぐには、帳簿上の理論在庫の仕組みと、倉庫内にある実在庫の間に生じる差異の原因を正確に理解することが不可欠です。
本記事では、理論在庫の定義と計算方法や実在庫と乖離が生じる原因、乖離を最小限に抑える最新の対策まで、現場目線で解説します。
理論在庫とは?
理論在庫とは何か?その定義を分かりやすく解説
理論在庫(英語:Theoretical Inventory)とは、商品の入荷、保管、出荷時に記録されたデータをもとに算出される在庫数です。過去の需要実績やリードタイム、安全在庫などの要素から「持つべき在庫水準」を計算した在庫管理の指標として用いられます。
一定条件下での持つべき在庫水準であり、将来の需要と供給バランスを最適化するための目標在庫とも言えます。
理論在庫と帳簿在庫の違いは?
「理論在庫」は、“理論的に導き出された最適在庫量”であり、企業が持つべき理想の在庫水準を示す有用な指標です。
一方で、「帳簿在庫」は実際の入出庫データや棚卸結果を記録し、“公式記録としての在庫数”を管理する役割を担います。
いずれも在庫管理には欠かせない存在ですが、両者が食い違うと正確な意思決定が難しくなります。
現場での棚卸やデータ入力を正確に行いながら、需要予測やリードタイムの変動を見極め、理論在庫と帳簿在庫を適切に活用することが理想的な在庫管理体制を築くカギとなります。
関連記事:「帳簿在庫」>>
参照記事 :「2023年;ものづくり白書」>>
理論在庫の計算方法
理論在庫の計算式
理論在庫とは、過去実績・販売計画・レシピ(製造業の場合)などから 「理論上あるべき数量」 を算出した在庫指標を指します。
実務では下式の発注点(Reorder Point)の計算式がよく使われます。
平均需要量 × リードタイム + 安全在庫
- 平均需要量:一定期間の需要を予測し、平均値をとる
- リードタイム:発注から納品までにかかる時間
- 安全在庫:予想外の需要変動やリードタイム遅延に対応するためのバッファ
ただし、この単純式だけでは理論在庫の算出値は精緻ではありません。近頃では、AIやIoTを活用したリアルタイム補正によって補完されるケースが増えています。
理論在庫に依存した在庫管理の課題
実在庫とは?
「実在庫」が実際に倉庫にある在庫数なのに対し、「理論在庫」はあくまで需要予測やリードタイム、安全在庫をもとに導き出す在庫指標となります。「理論在庫と実在庫」の差異から起こるリスクや、実際の運用で生じる課題を整理してみます。
理論在庫に依存した在庫管理のリスク
需要予測や安全在庫の計算式を用いて割り出した「理論在庫」は、あくまでも“理想値”に基づく在庫量です。しかし、実際の在庫状況はリードタイムの遅延や需要の急増など想定外の要因によって変化しやすく、発注数やタイミングが理論値どおりに合わなくなることがあります。
理論在庫に依存した在庫管理は、欠品リスクを高めたり、逆に在庫を抱えすぎて保管コストを圧迫する事態を引き起こします。
理論在庫が実在庫と乖離する3大要因
記録のタイムラグと誤差
在庫管理システムに入力するデータが誤っていたり、定期的な棚卸作業の頻度が少なかったりすると、在庫数の情報更新が追いつかずに理論値とのギャップが広がります。
紙媒体などを介し、手動で入力する在庫管理では、記録漏れや最新情報の反映に遅れが生じやすく、帳簿と実物に差が生じます。帳簿在庫の数値は理論在庫を算出するうえでも重要な要素であるため、帳簿と実在庫の乖離は理論在庫の歪みにつながります。
変動する需要とリードタイム
理論在庫は一定の条件下で成り立ちます。原則、商品ごと平均需要量とリードタイムに基づいて算出されるため、急な需要変化や納期遅延には対応できないケースがあります。理論在庫に依存した在庫発注・在庫管理では、欠品や過剰在庫に至り、機会損失や在庫圧迫による経営悪化につながります。
最終的にはコスト増大だけでなく、ブランドイメージの低下・信頼喪失という大きなダメージを招くリスクを抱えています。
情報の分断と属人管理
在庫管理や在庫発注、生産・販売計画に関わる営業・生産・購買などの部門間で在庫情報が共有されていないと、不要な発注や在庫切れの見落としが発生しやすくなります。情報の分断はアナログな在庫管理に限らず、デジタル化された在庫管理においても、情報共有手段が不十分であったり、教育が不十分であったりすることでも生じます。
また、在庫管理業務が標準化されていない場合には、業務の属人化が起こりやすいため、さらなる情報分断・業務の分断となるリスクが生じます。
理論在庫と実在庫の差異を解消する方法
IoTによる実在庫のリアルタイム把握
在庫管理の精度を高める第一歩は、実在庫の状況をリアルタイムで把握することです。スマートマットクラウドのようなIoT型在庫管理システムでは、重量センサーを活用し、物品の増減を常時計測・記録することで、人的作業を介さずに在庫情報を可視化できます。
これにより、在庫差異や発注ミスを未然に防ぎ、欠品・過剰リスクを抑えることが可能になります。
部門間の在庫可視化と棚卸業務改革
在庫の精度を高めるには、倉庫現場だけでなく営業・生産・購買といった他部門との連携も不可欠です。販売予測や発注情報を共有し、安全在庫の根拠を統一することで、無駄な在庫を減らせます。
また、棚卸にはバーコードやRFIDを活用し、差異が発生した際には即時報告と原因特定ができる体制を整えましょう。作業の標準化と属人化の排除も、安定した在庫管理を支える鍵となります。
AI需要予測との統合で理論在庫を最適化
従来の静的な計算式による理論在庫では、急な需要変動やリードタイムの揺らぎに対応しきれません。AIを活用することで、販売履歴や需要パターンを自動学習し、在庫水準を動的に補正できるようになります。
リードタイム補正やリアルタイム需要予測といった技術により、理論在庫の精度が飛躍的に高まり、安定した供給体制の構築が可能になります。
実在庫管理の重要性
理論在庫だけでなく実在庫をリアルタイムで正確に把握できる仕組みがあれば、発注タイミングをより精密に見極められるため、在庫回転率の向上につながります。
たとえば理論在庫数のみを基準に発注する場合、実際の在庫状況を反映しきれず、需要が増えたタイミングを逃して品切れ・過剰在庫のリスクがあります。リアルタイムで把握した実在庫数をもとにすれば、在庫が過剰になる前に発注回数やロットサイズを調整でき、結果として回転率が上昇します。
結果的に在庫コストの削減が可能となり、管理負荷や棚卸時の煩雑さも軽減されるため、全体的な生産性向上が期待できます。
理論在庫に依存しない在庫判断を実現 -- スマートマットクラウド
スマートマットクラウドとは?
「スマートマットクラウド」は、リアルタイムに実在庫を見える化する在庫管理システムです。マット状のセンサー機器を商品や資材の下に設置し、クラウドと連携することで重量の変化を常時モニタリングし、実際の在庫数を自動で集計・記録します。
従来の目視&手作業による在庫チェックや情報伝達の作業コストをかけることなく、最新の実在庫数を見える化します。
リアルタイム実在庫を測定
従来の棚卸では一定期間に一度しか在庫を把握できません。スマートマットクラウドを使えば“今どれだけあるか”をいつでも把握でき、在庫管理の精度と速度が飛躍的に向上します。
在庫差異の削減によるコスト削減
スマートマットの上に置いている商品の重量から自動測定するため、入力ミスや棚卸頻度の不足によるデータのズレを最小限に抑えられます。結果、無駄な在庫コストや棚卸差異の調整コストを削減することができます。
発注ミスを減らし、欠品や過剰在庫を防ぐ
常に最新の在庫数が把握できるため、「まだ在庫が十分あると思っていたら実は不足していた」という欠品リスクや、「見落としによる発注の重複で余剰在庫を抱える」リスクが減ります。販売機会を逃すことなく、保管コストも抑えられます。
作業効率向上・人的リソースの削減
手動での棚卸作業は時間と労力がかかり、人為的なミスを誘発しやすいのが難点です。スマートマットクラウドなら、日々の在庫把握作業や定期的な棚卸の回数を抑えられるため、スタッフはより付加価値の高い業務に時間を割くことができます。
データを活用した需要予測の精度向上
自動収集された在庫データは、販売動向や需要予測を分析するうえでも大きな武器になります。実在庫の変動から、需要が急増する時期や商品ごとの売れ行きパターンを精緻に読み取り、発注計画の精度を高めらることができます。在庫データは最適な在庫水準の維持に役立つだけでなく、経営判断の材料に活用できます。
理論在庫と実在庫の差異を解消したスマートマットクラウド導入事例
スマートマットクラウドの機能を活用して、理論在庫と実在庫の差異を解消した事例をご紹介します。
特許機器株式会社様の事例(製造業)
●対象副資材:センサー・ケーブル・金属加工品・基板など製品構成部材
●Before:実在庫の出入りを入出庫表へ記録、その後、システム上で理論在庫も更新し、棚卸の際に実在庫と理論在庫を照らし合わせ管理していました。理論在庫数と実在庫数の合致率が低かったことが課題でした。棚卸で判明した差異は遡って原因を調査する必要があり、そこにも時間と労力がかかっていました。
●施策:在庫部品の中で重要部品にスマートマットを導入。
●After:現物をカウントしなくても容易に実在庫数の確認が可能になりました。理論在庫と実在庫数のズレの見える化し、原因特定がしやすくなりました。原因に対処していくことで、理論在庫と実在庫数の差異を軽減、在庫精度向上を実現できました。
在庫精度向上により棚卸資産の仕損費拡大の防止、誤計上が起因となった過剰発注による廃棄ロスも予防できるようになり、キャッシュフローが良化しました。
株式会社カナエ産業様の事例(製造業)
●対象副資材:工業用ゴム部品の製造に使用する材料バッチ
●Before:現場から緊急の材料オーダーや、顧客からの特急の注文が原因で実在庫と理論在庫の差異が発生し、生産計画の遅れのリスクがありました。担当者だけが在庫状況を把握し管理が行き届かず、発注ミスや発注漏れ、過剰在庫の課題が発生していました。
●施策:保管用の棚にスマートマットを設置。
●After:受注や生産指示があった時に、本社から遠隔で在庫を確認し、発注まで行なうことができるようになりました。在庫が一度に動いた場合は状況を検知し、イレギュラーの消費なのか、ミスなのか迅速に原因を確認できる体制になりました。