在庫管理術
チョコ停【意味や定義、設備トラブルを含む数々の原因と対策】
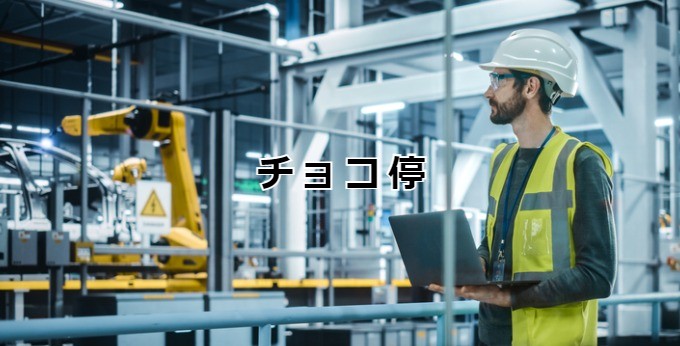
製造業で7大ロスの原因のひとつとされる「チョコ停」。こちらの記事では、チョコ停に関する定義や設備トラブルを含む数々の原因と対策を、分かりやすく解説します。
さらに稼働率との関係や計算方法、工場生産高や製品品質への影響についてご説明。またチョコ停が引き起こされる課題を解決するIoTソリューションを紹介しています。
チョコ停とは?【正式名称や定義】
チョコ停の定義
チョコ停とは製造業の現場で使われている用語で、正式には「生産設備を稼働中にちょこっと停止させた」状態を示す略語です。設備のトラブル発生や原料に異常*1があることで生産がストップ・空転する事象であるため「空転ロス」とも呼ばれています。
またチョコ停は、設備や原料にトラブルの原因があったとしても軽微な状態であり、現場スタッフのみで解決でき早期に復旧できるライン停止状態を意味します。そのため「ちょこっと停止した」時間も数十秒から10分程度*2の範囲を大きく逸脱しません。
また英語の正式名称はありませんが、「Short-time breakdown / Short-time breakdown in the production line」という表現が使われています。
*1:JIS(日本産業規格の生産管理用語)用語であるチョコ停は、設備故障における小故障として分類され、原料異常は含まれていない。しかし現状では、原料のコンタミ混入や仕掛品の品質が不均一なこともチョコ停の要因となっているため、当記事では設備小故障以外についても言及(JIS規格について詳細は後述)。
*2:製造業種や企業によって異なる。組立・組付など機械・自動車産業では5分までを目安に、医薬品や化学系プラントでは10分までを目安にしている例が見受けられる。
チョコ停ロスとは?|7大ロスのひとつ
製造業においては、生産効率を低下・阻害する7大ロスが上図のように分類されています。その中でチョコ停によるロスは、速度低下ロスと共に正味稼働時間内に発生する「性能ロス時間」に含まれます。
上記の7大ロスを「7つの設備ロス」として扱う業界もありますが、現実問題としてロスの内容は設備異常に限りません。例えば、原料に目視で確認でき手作業で排除できるコンタミが混入していたり、前工程から流れてくる仕掛品の品質にバラつきがあったりすると、チョコ停をしたり速度を下げたりして対応するケースがあります。
また医薬品・化学品・化学機能材・食品業界では、加工処理速度やラインの搬送速度が生産条件に含まれるケースが多く、速度低下やチョコ停は不良品発生に直結することも。この場合は不良ロス時間に相応し、歩留まり低下の要因として扱われます。このように全ての製造業界で、7つの設備ロスが正確に一致するわけではないことを覚えておきましょう。
チョコ停の原因
設備トラブル以外も空転ロスの原因に
次のような事象が発生すると設備不良や作業の支障が生じ、チョコ停に繋がります。
- 保全作業不足による装置・機械の動作不良
- 削りカス*3や粉体*3の堆積による作業障害や設備故障
- 装置・機械の清掃不足によるコンタミ混入
- 生産ラインへのモノの搬送量が不適切、過多
- 複数工程の場合、前工程の品質が不均一
チョコ停のほとんどが設備の保全不足・設備と資材や仕掛品の清掃不足が原因となって発生します。しかし資材搬送量の供給過多や仕掛品の品質にバラつきでもチョコ停は発生します。
*3:前工程で原材料を切削・裁断・圧縮・伸長した際に出るコンタミ
また生産効率向上や生産リードタイム短縮のために、さまざまな生産マネジメントがあります。機械の組立・組付工程での部品の配膳作業や、複数工程でモノの整流化を図る「一個流し生産」や「かんばん方式」などがそれに相当します。
しかし作業効率化を図る術であるにも関わらず、ヒューマンエラーによって配膳作業が滞ったり、モノの流れが澱んだりします。人的ミスをゼロにするのは不可能。そこからチョコ停が生じるリスクがあることは覚えておきましょう。
チョコ停の原因と対策
日常点検・保全作業不足
機械や設備に注入する潤滑油の差し忘れや、ボルト・ネジの増し締め忘れ、ベアリングやタイミングベルトの交換が不適切など、日頃行うべき点検や保全作業が不十分なことでチョコ停が引き起こされます。
設備や装置の特性に合わせて、稼働前ごとに点検・保全作業を怠らないように日々、努めるようにしましょう。しかしこの作業は保全スタッフではなく、生産現場の作業員が行うべきところです。
保全スタッフは現場作業員へ日常点検や稼働前の保全作業の重要性について説明し、またそれに費やす時間が取れるように、生産管理部門とも連携をとる必要があります。
清掃不足
一方で清掃不足は、削りカスやゴミが装置や設備内に挟まって動作支障を引き起こしたり、粉体が堆積しネジ穴などに詰まって作業に支障をきたしたりします。
また原材料にコンタミが混入し取り除く必要が生じることも。チョコ停の場合は目視でカンタンに確認でき、手作業で取り除けるレベルのコンタミ混入を示します。
本来はエアシャワー*4で粉体や削りカスを吹き飛ばしたり、装置等に付着しているコンタミの特性に応じて、シンナー清掃や水・アルコール清掃といった対策を採るべきところです。
*4:エアーノズルやエアーガンで圧力をかけた空気を噴射し、粉体や細小なゴミを取り除く作業
搬送量が不適切・過多
また複数工程で生産ラインが連結されている場合、僅かでもスループットに差があると、ボトルネック工程にまで陥らずとも、チョコ停が繰り返されるケースがあります。
スループットを均一にするか、ラインに中継地点やパーツフィダー*5を設けて適切な量を搬送するようにしましょう。
*5:「パーツフィダー」とはボウル型容器で大量の製作物を振動とアタッチメント動作により同一の向き・体勢に整えて次工程の生産ラインに供給する装置のこと。
前工程の品質にバラつき
同じく複数工程の場合、前工程の品質にバラつきがあると、次工程で余分な手間がかかり、作業を中断する場合があります。熟練工や手慣れた製品ならほぼ起こりえない現象ですが、新人スタッフの投入があったり、新規開発品の生産であったりすれば品質のバラつきが発生する可能性が大きくなります。
このような場合は必ず、次工程に搬送する前に品質チェックを行い、不良品や手直し品は予め取り除いておきましょう。
チョコ停とドカ停の違い
生産管理用語にチョコ停に似た「ドカ停」という用語があります。これは「ドカっと生産ラインが停止している」状態の略語。チョコ停とドカ停の最たる違いは生産ラインの再稼働、復旧までにかかる時間の差です。
チョコ停は数十秒から10分ほどの時間で復旧でき、装置や生産ライン全体に深刻な故障があるわけではありません。一方でドカ停は復旧に少なくとも1時間以上かかり、またシステム全体や装置に深刻なダメージがある大故障を示しています。
最悪な場合、装置やシステムの会社に連絡を入れ、修理や買い替えが必要となる場合も。さらに納期にも影響を及ぼし、複数工程の場合は前後の生産工程も稼働時間のロスになります。これらを防ぐためには、日頃の保全活動や頻発するチョコ停の集計・原因究明が不可欠です。
工場の計画停止時間内で行う保全活動で、計画的に装置・機械のメンテナンスや入れ替えを行えば、工場全体の生産高やさらには経営にも影響がでる「ドカ停」を防ぐことができるでしょう。
設備が次のいずれかの状態になる変化。a)規定の機能を失う・b)規定の性能を満たせなくなる・c)設備による産出物や作用が規定の品質レベルに達しなくなる。
備考:設備が生産ラインなどの大規模なシステムの一部となっていて、システム全体を停止に至らしめるような重大又は決定的な故障を大故障(通称としてドカ停)、逆に設備の部分的な停止又は設備の作用対象の不具合による停止で、短時間に回復できる故障を小故障(通称としてチョコ停)という。
日本産業規格(JIS)「生産管理用語」より引用
チョコ停の集計や計算方法
チョコ停の記録やデータ集計はなぜ必要?
チョコ停はおおよそ数十秒から数分でトラブルの原因を排除することができ、生産ラインの稼働再開までにそれほど時間を要しません。そのため余り重要視されず、目の前の生産を優先するあまり、チョコ停の原因分析や再発防止に取り組まない傾向があります。
また、たとえ作業員がチョコ停データの記録や集計の必要性を感じていたとします。しかしタクトタイム*6短縮に合わせムダを省いた作業導線や、シビアな生産ラインへの継続的な監視作業を鑑みると、現場作業員がデータ集計する時間的な余裕はほぼありません。
しかし頻発するチョコ停には大きな設備トラブルが潜在する場合があります。もしくは製品設計・新規開発品設計にやや無理がある、生産条件や生産ライン設計が非常に厳密である実態が隠れているケースも否定できません。
こういった原因究明のためには専門のスタッフやシステムを投入してでも、チョコ停を要因別に記録し、要因ごとに停止時間の回数と合計を集計しましょう。同じ理由でチョコ停が繰り返されるなら必ず原因を究明し、その場しのぎの緊急対応で終わらせずに、根本解決に至る改善を行うことが必須です。
ここ最近ではチョコ停の理由ごとに分類して、日次や製品ごとにデータを集計するIoTセンサ×IoTソリューション(ドライブレコーダーや分類・集計ボードなど)×上位集計システムといった形態のチョコ停の監視・改善アイテムが数多く販売されています。
*6:タクトタイムとは製品ひとつを生産するのにかかる時間。サイクルタイムとも言う。
チョコ停と稼働率の計算方法
チョコ停を含んだ稼働率を「TPM*7」の考え方に則って算出することができます。
工場の現場にスタッフが入り電源などを入れて稼働できる状態が「負荷時間」です。この時、日常保全・生産立ち上げ、生産後片付け・清掃といった調整時間を「計画停止時間」とし、また引継ぎや休憩などを「停止ロス時間」とします。
その上で、チョコ停を含んだ稼働率の計算方法は次のようになります。
*7:TPMとはTotal Productive Maintenanceの略であり、生産に関するあらゆるロスをゼロに近づける活動のこと。継続的な生産性向上と収益確保を実現する全社規模での生産革新活動として、日本では「全員参加の生産保全」と称されている。
例えば1日2交代の2班体制で朝礼・電源ON/OFF・終礼を差し引いた15時間が負荷時間とします。準備や片付け・保全活動にかかる計画停止時間が2.25時間でした。
またこの際の製品は、少なくとも最小ロット単位では連続生産が必要とします。問題なく生産している場合、基本的にラインを停めずに生産し続ける特徴があるとします。
そのため休憩は交代で取り、大まかな引継ぎは班長同士・細かい引継ぎは作業スタッフ同士で機械動作を注視しながら行う場合、停止ロス時間はゼロになります。
その場合の稼働時間は「負荷時間ー計画停止時間ー停止ロス時間」であるため、
15-2.25-0=12.75
となります。そのため稼働率は「稼働時間÷負荷時間」なので、
12.75÷15=0.85
となり、稼働率は85%でした。しかし稼働時間の間にチョコ停が4回あり、合計30分間停止していました。その場合の稼働率は「稼働時間÷(負荷時間+チョコ停時間)」で算出するため、
12.75÷(15+0.5)=0.822580....
となります。チョコ停がない場合より、稼働率が約3.8%低下したことが判ります。
チョコ停の影響範囲
高頻度なチョコ停は工場稼働率や品質に影響する
チョコ停の僅かな停止時間であっても頻度が高ければ、日次や月次で集計すると工場稼働率が予想以上に下がっていたという結果になりかねません。
さらに高頻度なチョコ停は装置・設備の深刻な問題の予兆や発現でもあります。いずれ「ドカ停」に繋がる大故障を引き起こせば、工場稼働率の大幅な低下に繋がります。
また前述したように、製品設計・新規開発品設計にやや無理がある、生産条件や生産ライン設計が非常にシビアであるのに、チョコ停を繰り返しながらも生産したとします。その場合、品質的には規格ギリギリでの製品生産である可能性が非常に高くなります。
そのため装置・設備トラブルやコンタミ混入以外で高頻度に発生するチョコ停は、製品の品質を見極める指標となります。さらには製品設計や生産条件を見直し、改善を行う判断基準としてもよいでしょう。
製品によってはチョコ停でも不良率や生産高に影響
機械の組立・組付や自動車・家電産業の工場では、チョコ停が起こったとしても時間的なロスは生じますが製品そのものがロスになることは余りありません。
但し、設備の不具合で製品自体が挟まったり、落下したりして破損すれば製品ロスとなるケースがあります。とはいえ不良品数は1~数個単位に留まるため、不良率が極めて高くなることは少ないでしょう。
ただし食品・金属・化学・繊維・印刷といった産業では、チョコ停が大きな製品ロスに繋がることも。ロット単位でチョコ停を繰り返せば、該当ロットの全数廃棄に繋がる製品不良も起こり得ます。
例えば食品産業では焼く・揚げる・蒸す・煮るといった加熱工程でチョコ停が起こると規定の加熱時間に過不足が生じ、不良品となる可能性があります。この場合、正規の商品とはならず廃棄されるかB級品として処理されます。
また金属産業で金属導線状の製品を、化学産業でチューブ状・ロール状の製品といったメートル単位で生産している際にチョコ停が生じたとしましょう。この場合、ロット単位*8とチョコ停が発生した場所によっては大きな製品ロスとなる可能性があります。
例えばロット単位が100Mの場合、99Mでチョコ停が発生し延伸や成形・機能付与のライン動作が停まれば、この99M分は製品とはなりません。
金属のように再び熔解させて原料を再利用できるなら、手直し*9ができるため製品・原料ロスには繋がりません。しかし化学産業で扱うゴムや塩化ビニル・プラスチック素材の製造・機能付与にはほぼ不可逆的な反応*10が用いられ、手直しができないなため製品ロスとなります。
また繊維産業や印刷業においては、かなり高速で印刷・紡績しているケースが数多く見受けられます。そのためチョコ停を繰り返すと、工場の生産高にもクリティカルな影響を引き起こします。
さらに紡績や印刷作業でもチョコ停の内容によっては、停止前後の製品の品質が規格外・ロット単位を満たさないなどの理由で、製品ロスとなる可能性は大きくなります。
*8:ロット単位とは製品の生産/販売における最小単位のこと。例えば1ロット=100個で3ロット受注なら、「300個の製品を生産し納入」するという意味。
*9:手直しが可能でも、手直しに掛った時間はロス時間として扱われる。
*10:この場合の不可逆的反応とは、UV照射や加熱により硬化したもの。いずれも化学業界では2液型樹脂/硬化剤/光開始剤などを用い、不可逆性が認められる。

チョコ停頻度を見える化する方法
生産現場の不良品や手直し品の置き場にIot重量計を設置
生産現場にIoT重量計を設置し、不良品や手直し品を置くことで生産時にどの程度の不良率となるかリアルタイムかつ遠隔で把握することできます。
クラウドを介しデータを転送することで不良品集計も瞬時に行えるため、早期のリカバリー生産や手直し作業への対応が可能。納期調整の工数の削減にも寄与します。
さらにチョコ停で発生した不良品・手直し品がIoT重量計に置くだけで、どのようなタイミングで発生したか、また1製品あたりの発生頻度もカウントできます。
チョコ停要因を抑制するには?
IoT重量計で配膳に関する人的ミス削減・適正な配膳作業をサポート
部品の配膳作業にIoT重量計を用いれば、工程での配膳キットの消費スピードを見える化。現場の配膳キット棚やキットの空箱置き場にIoT重量計を設置するだけで、コミュニケーションコストを掛けることなく、作業の進捗度合いを把握できます。
また複数工程や多品種少量生産・変種変量生産など、配膳工数が多く煩雑な生産体制であっても、消費スピードから常に適切な量のキット数を予測し、効率のよい配膳作業をサポートします。
また重さにより部品間違い、キットの配置間違いなどのヒューマンエラーを検知。組立・組付作業のチョコ停に直結する、部品キットの配膳遅延や部品・キット間違いを防いでくれます。
チョコ停を繰り返す工程を特定「スマートマットクラウド」
スマートマットクラウドはリアルタイム実在庫の見える化で在庫管理、工程カイゼン・DXを進めるIoT SaaSプロダクトです。IoT重量計(スマートマット)で在庫管理はもちろん、工程内で発生した不良品や手直し品のリアルタイム数量管理が可能です。
現場でのモノの動きを捉え、「チョコ停」などの生産トラブルをコミュニケーションコストを掛けずに把握可能。リカバリー生産や手直し作業のスケジューリングなど生産管理における早期対応ができます。
スマートマットクラウドはシンプルな「重さの変化」を捉えてデジタル・ネットワーク化し業務変革できるDXを実現。そのためリアルタイム実在庫データを武器に、現場のさまざまなモノと情報を可視化し活用できます。
数えにくい液体・粉体状の資材やチューブ・ロール状の仕掛品や製品も重さにより正確にカウント。不良品・手直し品をマットに置くだけで集計できるため、あらゆる対応をスピーディーに進められます。スマートマットはサイズ展開も豊富でg単位からマルチマット使用で数百kgまで対応!
さらに配膳作業にIoT重量計を用いることで、配膳作業の効率化にも寄与。リアルタイム計測で配膳キットの消費スピードが把握できるため、適切タイミングで必要な工程に配膳作業が行えます。また重量データにより配膳ミスや部品間違いの早期発見が可能です。
◆特徴
- 遠隔で在庫を一元管理:倉庫や各拠点の在庫を管理画面で一元管理
- 工程間のモノの流れを把握:コミュニケーションコストを掛けずに生産調整が可能
- 重量による正確なカウント:不良品や手直し品数量のリアルタイム集計と早期対応
- 配膳作業の効率化:消費スピードを把握し、適切なタイミングで必要な工程に配膳
- AI x IoTで在庫最適化をし続けられる:大量データをAIが監視・解釈・検知。問題をタイムリーに抽出して改善を提案