在庫管理術
ボトルネック工程【意味や見つけ方、改善方法について解説】
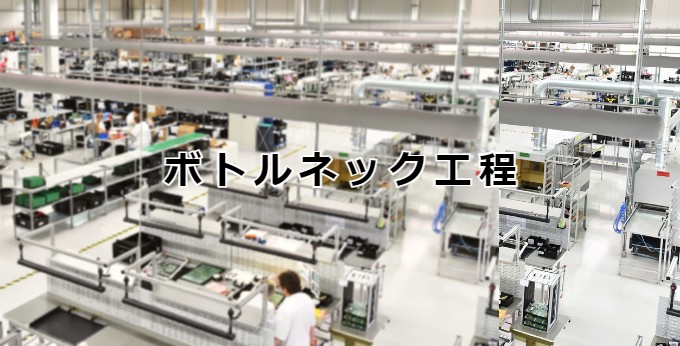
こちらでは、製造業におけるボトルネック工程の意味や見つけ方、ボトルネックの制約条件を解消するマネジメント手法であるTOC理論を用いた改善について説明します。
また定常的なボトルネック工程に限らず、突発的なボトルネック工程の早期発見に寄与するIoTソリューションをご紹介。複数工程管理の課題解決にぜひ役立ててください。
ボトルネック工程とは?
複数工程の中で生産出来高が特に低くなる工程をボトルネック工程と言います。
瓶(ボトル)の本体(ボディ)に比べて細くなっている首(ネック)部分が吐出量を制限するように、複数工程の生産において極めてスループット*1が低くなっている工程を示す用語です。
ボトルネック工程がある場合、その他の工程がどれほど生産力が高くとも、全体ではボトルネック工程の出来高に見合った数量でしか製品が生産されません。例えば下図のような複数工程の場合、スループットの低い「工程④」の制約が全体にかかり、最終的な製品の出来高は工程④と同じ400個/時間となります。
*1:スループットとは処理能力や処理スピードのこと。製造業においては1時間ごとの生産出来高で示す場合が多い
複数工程の管理|生産管理で工程表やシステムを用いる
製造業で複数工程を管理するには、まずBOMや製品仕様書、作業標準書を基に工程表を作成します。生産管理システムの導入などデジタル活用している製造業もあれば、エクセルやホワイトボード、紙媒体などアナログな手法を使っている製造現場もあります。
但し、ベースとなるのはいずれも工程ごとに必要な原料や時間、ある程度のオペレーション内容をまとめて一覧表示した工程表です。
複数工程の場合は特に、それぞれの生産リードタイムや仕掛品の移動、各原料の搬入、ロットごとのタクトタイムの把握などの管理が煩雑となります。そのため生産管理システムの導入に留まらず、さまざまな業務でDXが推進されています。
ボトルネック工程の見つけ方
ボトルネック工程を洗い出すには?具体的に解説
ボトルネック工程の見つけ方としては、次の3通りが代表的です。
- 仕掛品の流れの澱み。滞留・分散の有無
- 作業員の手待ちの発生の有無
- 他工程に比べた際の稼働率の高さ
複数工程のなかでボトルネック工程がある場合、上図のような仕掛品の滞留や作業の停滞によってボトルネック工程を特定することが可能です。
前工程が終了した仕掛品が滞留したり、仮置き場に置ききれずに分散したりと、ボトルネック周辺では仕掛品が溢れて澱みが生じます。反対にボトルネックの後工程では、仕掛品が流れてこず、作業が中断するなど作業員の手待ちのムダが発生します。
これら以外にも、他工程と比較して極めて稼働率が高ければ、ボトルネック工程である可能性が大です。他工程で7~8割程度の稼働率に対し、95%以上の稼働率であるなら、生産効率が良いわけではなく、生産が他工程に追いついていない場合があります。
また稼働率が異常に高いと、生産以外に掛かる搬入や設備点検・品質チェック・搬出に適切な時間を掛けられなくなるリスクがあります。品質異常の発生やモノや情報の滞留など、ボトルネック工程によって更なる悪循環を産んでいる可能性も否定できません。
ボトルネックに陥りやすい工程とは?
スループットの問題だけでなく、ボトルネックに陥りやすい要因を孕む工程もあります。
- 人員配置変えや新人配属をした当初の工程
- 設備を入れ替えた工程
- 小規模トラブルが多発する工程
人員の配置換えや新人を配属した工程は指導や訓練に人と時間を費やし、どうしても生産効率が低下しがち。そのため配置・配属当初はボトルネック工程になり得るとして、リスクヘッジの観点からも注目しておくとよいでしょう。
設備の入れ替えも同様で、同じような機械・パーツ・操作基盤であったとしても、ネジの位置や潤滑油の投入口がやや異なったり、操作ボタンの配置等が異なったりします。そうすると稼働前の点検や稼働操作に少しずつ遅れが生じ、生産効率が低下します。
また小規模トラブルが多発する工程には次のような要因*2があると考えられます。例えば加工条件の難易度が高い、または加工スピードが速くスタッフの作業速度と拮抗しているなら、ヒューマンエラーが引き起こされやすくなります。
他にも装置や説備の扱いに精緻さが必要であれば、違和感程度の小さなミスがトラブルに繋がる場合も。さらに装置や設備の経年劣化によっても小故障が発生するケースも否定できません。
*2:これらすべての要因により、チョコ停(生産における機械設備が僅かな時間だけ停止すること)が繰り返される可能性が大。チョコ停を放置しておくと、大幅な仕切り直しや設備の深刻な故障に繋がるケースがあります。
ボトルネック工程を解消するには?
「TOC理論」における継続的改善プロセスが有効!
ボトルネック工程は、TOC理論*3に沿った継続的改善プロセスで解消できる見込みがあります。TOC理論とは、英語で「Theory of Constraints」と表し、直訳すると制約条件の理論。製造業の複数工程に限らず、あらゆる業界の一連業務のマネジメントに用いられています。
ボトルネック工程のように何かしらの制約があり、パフォーマンスが著しく低下している条件やオペレーション内容に集中して改善策を打ち出すことで、最大限の改善効果を期待できるマネジメント手法を体系化したのが「TOC理論」です。
全体の底上げを実施するマネジメントとは異なり、制約条件に集中した改善・カイゼンであるため、最小限の時間とコストで効果が出る点がメリットです。制約を解消するには、次の「5段階集中プロセス」の各ステップを踏み、繰り返していきます。
- Step①:ボトルネック工程の制約条件を見つける
- Step②:特定した制約を既存リソース内で解消できるかを施策
- Step③:工場全体でStep②に従属、調整
- Step④:新たなリソースを投入し制約の解消を試みる
- Step⑤:Step①から④を繰り替えす
*3:イスラエルの物理学者、エリヤフ・ゴールドラットが開発したマネジメント理論。(Wikiより)そもそも製造業における「ボトルネック」の考案者でもある。一連業務のなかの制約条件を集中的に改善する手法を製造業以外の分野にも展開できるマネジメント体系として確立した。
製造業のTOC理論を用いたマネジメント方式を具体的に解説>>
ボトルネックは突発的な発生も有り
定常的なボトルネック工程を改善しても、ある工程で突発的なトラブルが発生すると、その制約を複数工程全体が受けます。通常では問題のない工程が、突如としてボトルネック化することは複数工程の生産プロセスで常に抱えている課題です。
このような突発的なケースでは、どの工程でトラブルが発生しボトルネックとなっているかを迅速に発見し、早期対応することは難しくなります。日次の最終確認でフタを開けてみれば、「今日、実は〇〇工程で機械トラブルがあり、本日の生産高は通常の50%以下です。」ということが全く無いわけではありません。
そうなると納期遅れや大幅な残業の発生にも繋がります。しかし突発的なボトルネックによる工場全体への影響を、人力で最小限に食い止めるのは労力が非常に大。複数の工程間で作業員の動きに無駄がないか、モノと情報の流れに澱みがないかなど、生産管理部門が常に監視しなければならないと負担が強いられます。
ボトルネック工程の有効な解消方法
リアルタイムで突発的なボトルネック工程を特定
複数工程において各工程の資材、仕掛品の一時仮置き場にIoT重量計を設置し、前工程から流れてきたモノや作業が完了したモノをIoT重量計に置くだけで、モノの分量や流れをリアルタイムで把握することが可能です。
遠隔からでもモノの流れが把握できるため、仕掛品の滞留箇所や僅小箇所を管理画面のモニターから素早く検知。突発的なボトルネック工程をリアルタイムで把握でき、早急な対応に寄与します。また各工程にモニターを設置することで、コミュニケーションコストをかけずにお互いの進捗度合いを確認できます。
IoT重量計を各工程に設置すれば、わざわざ現場に行って作業員の動きやモノの流れを把握するために走り回ったり、監視カメラに張り付いて作業スタッフの作業導線を監視したりする必要はもうありません。
ボトルネックへのサポートや仕掛品の入出庫量を速やかに対処する
突発的なボトルネック工程でもリアルタイムで把握できれば、仕掛品を整理したり、適切な量を運搬したりする要員やネック工程での軽作業要員などサポートスタッフを迅速に派遣することが可能です。
生産の統括部門がそのような対処や調整を行うことで、ボトルネックに該当する工程のスタッフはトラブル対応や生産オペレーションに集中できるでしょう。
さらには前工程の生産量を抑える、もしくは別製品への製造に切り替えるなどの指示を速やかに出せれば、突発的なトラブルに生産全体が大きく影響を受けることはありません。またボトルネックの後工程には別製品の製造指示や保全・5S活動などの指示を出せば、手待ちのムダを排除することができます。

ボトルネックを可視化する「SMC」
*SMCとは在庫管理システム「スマートマットクラウド」の略称
スマートマットクラウドはリアルタイム実在庫の見える化で在庫管理、工程カイゼン・DXを進めるIoT SaaSプロダクトです。IoT重量計で在庫管理・入出庫・発注を自動化。さらに現場でのモノの動きも捉え、工程間のモノの流れを分析し問題を見える化します。
シンプルな「重さの変化」をデジタル・ネットワーク化し業務変革に用いるDXとして、リアルタイム実在庫データを武器に、現場のさまざまなモノと情報を可視化し活用。工程をまたぐモノと情報の流れの澱みも特定します。
定常的なボトルネック工程の洗い出しはもちろん、突発的なボトルネック工程の早期発見など、工場の生産高に直接かかわる制約の解消、生産効率や現場力の向上に寄与します。
さらにスマートマットクラウドは生産工程の各進捗状況も可視化。生産管理部門に管理者システムを、生産現場に閲覧モニターを設置することでコミュニケーションコストを掛けることなく工場全体で工程の進捗度合いを把握できます。
後工程からひとつ前の工程に、必要な部品を、必要なタイミングで、いくつ必要かを自動で伝えることで、製造業の生産プロセスに潜むさまざまな課題を解消します。
◆特徴
- 遠隔で在庫を一元管理:倉庫や各拠点の在庫を管理画面で一元管理
- 需要に見合った供給を実現:ひとつ前の工程に伝え、過不足なく生産できる
- 仕掛品の流れを可視化:リアルタイムで仕掛品の滞留箇所や僅少箇所を検知
- 工程進捗の把握:コミュニケーションコストを掛けずにリアルタイム&工場全体で把握