在庫管理術
なぜなぜ分析|報告書は「証拠」で書く。上司を納得させるトヨタ式の本質と実践法
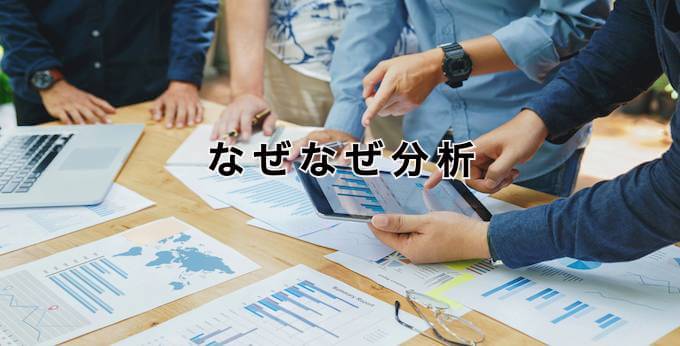
あなたの「なぜなぜ分析」が同僚から個人攻撃と受け止められたり、「これは個人の感想だよね?」と報告書を突き返されたりする根本原因は、分析に客観的な証拠が欠けているからです。
この記事では、トヨタ式の本質を学び、単なる分析手法だけでなく、誰からも納得される事実報告書を作成する技術を解説します。
この記事を読めば、以下の点が明確になります。
- なぜなぜ分析が意味がない「個人攻撃」に陥る本当の理由
- トヨタ生産方式の思想に学ぶ、問題の「真因」に到達する本質
- 明日から使える、客観的な証拠に基づいた分析報告書の書き方
\耳から学ぶ👂ポッドキャスト/
🎵音が流れます
なぜなぜ分析とは?
なぜなぜ分析とは、「なぜ(Why)」を繰り返すことで問題の根本原因(Root Cause)を追求する分析手法です。一般になぜを5回繰り返すと言われることから「5Why分析」とも呼ばれています。
なぜなぜ分析はトヨタ生産方式の中で体系化されましたが、現在では製造業にとどまらず、医療、IT、建設、サービス業などさまざまな分野で広く活用されています。
関連記事:「カイゼン」>>
関連記事:「ジャストインタイム」>>
「なぜなぜ分析」はなぜ失敗するのか?
失敗を招く3つの罠
頻発するトラブルを前に、なぜなぜ分析を試みたところ議論が紛糾し、後味の悪い結論で終わってしまった。こんな経験はありませんか?
良かれと思って始めたはずのなぜなぜ分析が、いつの間にか個人の責任追及になっていたり、そもそも問題の捉え方がズレたりするケースは、残念ながら非常に多く見受けられます。
なぜなぜ分析が失敗に終わる原因は、突き詰めると以下の3つの罠に集約されます。
【罠1】犯人探し=個人攻撃で終わる
なぞなぞ分析で最も陥りやすいのが、個人攻撃の罠です。
分析を進める過程で、「なぜ失敗が発生したのか?」という問いが、個人のスキルや注意力の問題に終始してしまうケースがよく見られます。
こうした場合、「次回から気をつける」といった精神論に終始しやすく、実践的かつ継続的な再発防止策には結びつきません。その結果、チーム全体の雰囲気が悪化し、メンバーが意見を出しづらくなるなど、生産性低下の悪循環に繋がります。
【罠2】最初の問題設定から思い込みで進める
「原因はおそらくこれだろう」といった先入観や仮説に基づいてスタートしてしまうと、その後の分析活動すべてがその仮説を裏付けるためだけの作業に終始してしまいがちです。
たとえば、「製品の傷は作業員の取り扱いが雑だったから」と決めつけて分析を始めてしまうと、作業方法以外の要素である設備・材料・環境などに潜む真因を見落とすリスクがあります。
【罠3】なぜの連鎖で論理が飛躍している
複数の事象を安易に結びつけてしまい、因果関係が曖昧なまま分析が進む場合があります。
例を挙げます。「なぜ機械が止まった?」→「部品が壊れたから」→「なぜ壊れた?」→「作業員の点検が不十分だったから」といった形で原因をたどる分析は、一見論理的に思えることがあります。
しかし部品が壊れた本質的な要因は、点検不足ではなく部品自体の設計寿命にあった可能性も考慮する必要があります。このように、客観的な事実やデータに裏打ちされていない推論を重ねてしまうと、本来の原因からかえって遠ざかってしまいます。
なぜなぜ分析の本質とは?トヨタ生産方式の思想に学ぶ
では、どうすればこれらの罠を避けられるのでしょうか。その答えは、この手法の原点であるトヨタ生産方式の思想にあります。
トヨタが本当に伝えたかったこと
なぜなぜ分析を生み出したトヨタ自動車元副社長の大野耐一氏は、その著書の中で次のように述べています。
トヨタ生産方式の二つの柱は、ご存じのようにジャスト・イン・タイムと、もう一つのニンベンのついた自働化である。(中略)この自働化という考え方は、単に機械を自動化することとは意味が違う。機械といえども、人間の知恵を働かせることによって、異常の判断ができるようにくふうすることをいうのである。
出典:大野耐一 著『トヨタ生産方式――脱規模の経営をめざして』(ダイヤモンド社)より引用
ここで重要なのはニンベンのついた自働化という考え方です。
これは、異常が発生したら機械が自ら止まり、問題を知らせる仕組みを指します。
つまり、トヨタ生産方式の根底にあるのは、問題が起きた際に個人を責めるのではなく、異常を検知して知らせる仕組みを構築し、改善するという思想なのです。
なぜなぜ分析も、この思想の上に成り立つツールであり、その目的は「真因」としてのシステム上の問題点を見つけ出すことにあります。
回数「5回」は目安
「なぜを5回繰り返す」に着目されがちですが5回という数字は、表面的な事象から真因にたどり着くための一つの目安に過ぎません。
なぜなぜ分析では、回数ではなく、「もうこれ以上は分解できない」という根本的な原因(真因)にたどり着くまで、事実に基づいて掘り下げる姿勢に重点を置きます。
【証拠主義】上司を納得させる「なぜなぜ分析」の正しいやり方 5ステップ
ここからは、トヨタ式の本質を踏まえ、上司や関係者を納得させるための具体的な分析の進め方を5つのステップで解説します。すべてのステップに共通する鍵は証拠主義です。
ステップ1:問題を定量的に定義する
まず、問題を誰が見ても同じように理解できるよう、客観的な事実で定義します。 「製品の傷が多い」といった曖昧な表現ではなく、
- いつから(例:8月1日以降)
- どこで(例:第二製造ラインで)
- 何が(例:製品Aの表面に傷)
- どれくらい(例:不良率が2%から5%に増加)
というように、5W1Hを使って定量的に記述します。
ステップ2:「なぜ」を問い、客観的事実で答える
次に、定義した問題に対して「なぜ」を問いかけます。
そして、その答えは必ず「〇〇という事実があるから」という客観的な根拠、すなわち証拠を伴っていなければなりません。
例えば、「なぜ不良率が増加したのか?」→「(証拠:稼働記録データより)第二ラインの装置Bの稼働時間が20%増加したから」というように繋げます。
ステップ3:根本原因「真因」を特定する
ステップ2を繰り返し、これ以上分解できない根本的な原因「真因」を特定します。真因は多くの場合、仕組みやシステムの不備に行き着きます。
例えば、「担当者がマニュアルを確認しなかった」は個人の問題ですが、「マニュアルが更新されておらず、古い情報だった」は情報管理システムの不備、すなわち真因である可能性が高くなります。
ステップ4:再発防止のための「対策」を立案する
特定した真因に対して、「どうすればその問題が二度と起こらないか」という観点で具体的な対策を立案します。
頑張る、注意するといった精神論ではなく、「〇〇という仕組みを導入する」という具体的な行動計画に落とし込みます。
ステップ5:対策の効果を測定し、標準化する
対策を実施したら、必ず効果測定を行います。ステップ1で定義した問題が、対策によってどれだけ改善されたかを同じ指標で評価します。効果が確認できれば、その対策を標準的な業務プロセスとして定着させます。
●筆者の経験からの一言アドバイス
【結論】: 全ての「なぜ」の答えに、客観的な証拠を紐づけること。私はこれを「1つのなぜに、1つの証拠」と呼んでいます。
私自身、品質保証部リーダーになりたての頃、なぜなぜ分析の報告書を「君の感想文は要らない」と上司に突き返され続けた苦い経験があります。転機となったのは、上司の「『なぜ』の答え一つひとつに、証拠はあるのか?」という厳しい一言でした。
それ以来、私は全ての分析において、例えば稼働記録ログや作業マニュアルの版数、担当者へのヒアリング議事録といった証拠を揃えることを徹底しました。
「証拠の鎖」を作ることこそが、なぜなぜ分析を主観的な責任追及から、客観的事実に裏付けられた分析プロセスへと高めるただひとつのカギとなります。
単なる分析で終わらせない。信頼性を担保する報告書の作り方
なぜなぜ分析の最後のステップ、それは報告です。
いくら優れた分析を行っても、そのプロセスと結論が他者に正しく伝わらなければ意味がありません。そして、ここで要となるのが「出典」の概念です。
その根拠はどこに?「出典」のない報告書は感想文
情報の出所、つまり出典を明示することは、読み手による検証を可能にし、その情報全体の信頼性を担保する上で不可欠です。
報告書を読んだ上司が知りたいのは、個人の意見ではなく、客観的な事実です。
分析の各ステップで用いたデータや情報について、その根拠はどこにあるのかを明記することで、報告書は主観的な印象ではなく、客観的な証拠と根拠に基づいた「事実報告書」へと進化します。
「引用」と「転載」の違いを理解し、著作権法を遵守する
報告書作成にあたり、他者の資料やウェブサイトの情報を参考にする場合、コンプライアンスの観点も重要です。引用と転載の違いを確認しておきましょう。
-
引用:自説を補強するために、他者の著作物の一部を正当な範囲で利用すること。出典明記が必須。
-
転載:他者の著作物を複製し、再公表すること。原則として許諾が必要。
社内文書であっても、これら著作権ルールを遵守する意識を持つことが、ビジネスパーソンとしての信頼性を高めます。
【事例】感想文から事実報告書へ。品質問題を解決した具体例
ここでは、私が過去にコンサルティングで関わった「ギアの摩耗問題」を例に、分析がどう変わるかを見ていきましょう。
【Before】担当者の記憶に頼り、「個人攻撃」に陥った失敗分析
• 問題: ギアの摩耗が原因で、装置Aが頻繁に停止する。
• なぜ①: なぜ摩耗する? → 潤滑油が劣化したから。
• なぜ②: なぜ劣化した? → 交換されていなかったから。
• なぜ③: なぜ交換されなかった? → 担当者のAさんが忘れていたから。
• 結論: Aさんの責任感が不足している。再発防止策は「Aさんへの厳重注意」。
この分析では、何の証拠もありません。すべてが担当者へのヒアリングに依存しており、結論は個人攻撃に着地しています。これでは、Aさんの不満が高まるだけで、根本的な解決にはなりません。
After:「作業記録ログ」を出典とし、真因を特定した成功分析
問題: ギアの摩耗が原因で、装置Aが頻繁に停止する(出典:装置稼働ログ)。
なぜ①: なぜ摩耗する? → 潤滑油の粘度が基準値を下回っているから(出典:潤滑油サンプル分析レポート)。
なぜ②: なぜ粘度が低下した? → 規定の交換サイクルを超えて使用されていたから(出典:保全部門データベースの作業記録ログ)。
なぜ③: なぜ交換されなかった? → 交換時期を知らせるアラートが作動していなかったから(出典:アラート作動履歴)。
なぜ④: なぜアラートが作動しなかった? → 3年前のシステム更新時に、当該アラートの設定が移行されていなかったから(出典:システム更新時の仕様書)。
結論: システム更新時の設定移行漏れ(仕組みの問題)が真因。 再発防止策は「全装置のアラート設定の総点検と、更新時チェックリストへの追加」。
●筆者の経験からの一言アドバイス
【結論】このAfterの事例こそが、私が提唱する「証拠の鎖」です。
この分析報告書を提出した際、議論は一切紛糾しませんでした。なぜなら、そこに書かれているのは私の意見ではなく、誰もが否定できない事実の連鎖だからです。
担当者の記憶という曖昧なものではなく、「データベースのログ」という客観的な証拠を出典として提示したことで、議論の余地なく仕組みやシステムの問題であると証明することができました。
客観的な証拠に基づくことで、無用な対立を回避し、円滑に建設的な改善アクションへと移行することが可能になります。
なぜなぜ分析に関するよくある質問(FAQ)
Q. どうしたら個人攻撃になってしまうのを回避できますか?
A. 最も効果的な方法は、分析の主語を人から仕組みに強制的に変えることです。
「なぜ担当者はミスをしたのか?」ではなく、「なぜシステムは担当者のミスを防げなかったのか?」と問いの立て方を変えるだけで、視点が建設的な方向へ変わります。
Q. なぜはどうして5回なのですか?トヨタ以外の事例はありますか?
A. 5回という回数は、トヨタ生産方式を確立した大野耐一氏が、自身の経験から「5回ほど繰り返せば真因に行き着くことが多い」と述べたことに由来します。 あくまで目安で、問題によっては3回で終わることもあれば、10回以上掘り下げることもあります。回数に固執せず「これ以上分解できない根本的な原因か?」を自問することが重要です。
Q. なぜなぜ分析が適さない問題はありますか?その場合の代替手法は?
A. あります。
なぜなぜ分析は、単一の原因から結果に至る直線的な因果関係を掘り下げるのに適しています。一方で、複数の要因が複雑に絡み合って発生する売上不振や顧客満足度の低下などの問題にはあまり向きません。複数の要因を網羅的に洗い出す場合は「特性要因図(フィッシュボーンチャート)」などの手法がより効果的です。
【まとめ】分析を事実に変え、明日からの行動を始めよう
本記事では、なぜなぜ分析が失敗する原因から、その本質、そして上司を納得させるための「証拠主義」に基づいた実践方法までを解説してきました。
もう一度、重要なポイントを振り返りましょう。
• 失敗の原因: 「個人攻撃」「思い込み」「論理の飛躍」は、手法の本質を見失うことで起こります。
• 本質: なぜなぜ分析の目的は、証拠に基づき、再発防止のための「仕組み」の真因を突き止めることです。
• 成功の鍵: 「1つのなぜに、1つの証拠」。分析のすべてのステップに客観的な証拠を紐づけましょう。
• 信頼される報告書: その鍵は「出典」の明記にあります。これにより、あなたの分析は主観的な感想から客観的な事実に変わります。
ここまで解説した分析ポイントを、あなたの職場で起きている課題解決にぜひ役立ててください。次回の報告書が、誰からも認められ、建設的なアクションに繋がることを心から願っています。
なぜなぜ分析×IoTでデータドリブンな現場改善へ
重量IoTソリューション「スマートマットクラウド」を併用することで、なぜなぜ分析を根拠を持った実践手法へと進化させることができます。
スマートマットクラウドは現場のあらゆるモノの流れをIoT重量センサで見える化し、発注を自動化し、補充や棚卸を超効率化する在庫管理のDXソリューションです。スマートマットの上に管理したいモノを載せるだけで設置が完了。
あとはマットが自動でモノの在庫を検知、自動計測します。自動計測されたデータはクラウド上に転送。リアルタイムの在庫消費データを記録し、管理。管理画面から、在庫量の推移グラフや在庫期間・在庫金額の表示によりさまざまなデータ活用が可能です。
なぜなぜ分析への活用例
① 在庫補充ミスの原因分析
→ 「なぜ補充が遅れた?」→「なぜ在庫数が見えなかった?」→「なぜ手動集計に頼っていた?」→ スマートマットで自動検知に切り替え
② 工程間トラブルの再発防止
→ リアルタイム実在庫の把握 × 自動発注連携によって、工程間の連携ミスを見える化&未然防止
スマートマットクラウドの基本的な機能
さまざまな自動発注に対応
お客様の発注先に合わせた文面でメール・FAXの送信が可能です
在庫圧縮を促進
推移を把握できるグラフで適切な在庫量を判断し、在庫圧縮を促進します
置く場所を選びません
スマートマットはA3サイズ〜A6サイズまでの4サイズ展開。ケーブルレスで、冷蔵庫・冷凍庫利用も可。
API・CSVでのシステム連携実績も多数
自社システムや他社システムと連携を行い、より在庫管理効率UPを実現します。
リアルタイム実在庫のデータを収集、分析、遠隔管理が可能
IoTで現場のモノの動きを捉えるため、生産工程内のリアルタイムなモノの流れを可視化します。そのため問題の分析・見える化に有効。リアルタイム実在庫データを武器に工程を跨ぐ流れの澱みを特定し、現場力の向上に寄与します。
また一方で、在庫置場に出向くことなくリアルタイムで管理画面から部品と仕掛品の在庫数を確認できます。在庫確認や補充タイミング把握のため、倉庫や工場内を走り回る必要はもうありません。