在庫管理術
VE(バリューエンジニアリング)【意味をわかりやすく・基本原則・手法・手順・事例など】
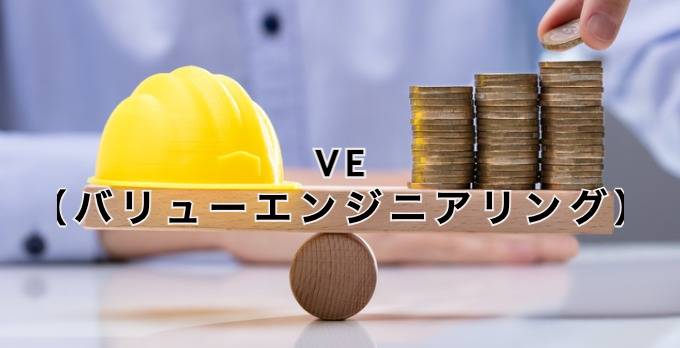
この記事では、VE(バリューエンジニアリング)の意味や定義をわかりやすく解説するとともに、その歴史や原則、手法、効果などを具体的に説明していきます。
VE(バリューエンジニアリング)とは
バリューエンジニアの意味をわかりやすく
VE(Value Engineering:バリューエンジニアリング)とは、日本語では「価値工学」と訳されます。
ITパスポート用語辞典(ITパスポート試験*に特化した用語集)に、次のように明記されています。
”製品やサービスの「価値」を、それが果たすべき「機能」とそのためにかける「コスト」との関係で把握し、システム化された手順によって最小の総コストで製品の「価値」の最大化をはかる手法”
また公益社団法人日本バリュー・エンジニアリング協会によって、バリューエンジニアは、下記のとおり定義されています。
”最低のライフサイクルコスト*で必要な機能を確実に達成するために、製品とかサービスの機能的研究に注ぐ組織的努力である”
わかりやすく簡単に言うと、製品やサービスの価値を「コスト」と「機能」の面から見直し、両方を改善することによって価値を高めていく手法や組織的努力と言えるでしょう。
また、VE(バリューエンジニアリング)は、VA(Value Analysis:バリューアナリシス)価値分析と呼ばれることもあります。
*ITパスポート試験:平成21年4月から新たに情報処理技術者試験に追加された、情報に関する国家試験の一つ。ITとは、Information Technology(インフォメーション・テクノロジー)のこと。
*ライフサイクルコスト(LCC):製品やサービス、施設、建築物などを製造あるいは利用するに当たって、そのライフサイクル(構想・企画・研究開発、設計、生産・構築、調達、運用・保全、廃却)のすべてにわたって発生する総コストのこと。
VE(バリューエンジニアリング)の経緯
VE(バリューエンジニアリング)は、1947年、米国・ゼネラルエレクトリック(GE)社の技師L.D.マイルズによって開発されました。当時は第二次世界大戦直後でさまざまな資材が不足しており、必要な資材の代替策としてバリューエンジニアリングは生み出されたとされています。
日本には、1960年頃に導入されました。 当初は製造メーカーの資材部門に導入され、そのコスト削減の成果の大きさに注目が集まりました。以降、企画、開発、設計、製造、物流、事務、サービスなどへと適用範囲が広がり、さまざまな業種で活用されるようになって現在に至っています。
VE(バリューエンジニアリング)の基本原則
VE(バリューエンジニアリング)をスムーズかつ効果的に進めていくためには、まずは以下の5つの基本原則を知ることが重要です。
- 使用者優先の原則
顧客(ユーザー)はどのような機能を求め、何に価値を置いて、何を必要としているか追及する。 - 機能本位の原則
果たすべき機能を明確にして改善する。 - 創造による変更の原則
固定概念にとらわれず、自由な発想や工夫により工夫・改善する。 - チームデザインの原則
各分野から知識や技術・経験を集めて、チームで改善を図る。 - 価値向上の原則
機能とコストの関係を分析し、価値を高める。
VE(バリューエンジニアリング)の手法
VE(バリューエンジニアリング)における価値、機能、コストの関係は、以下の式によって表されます。
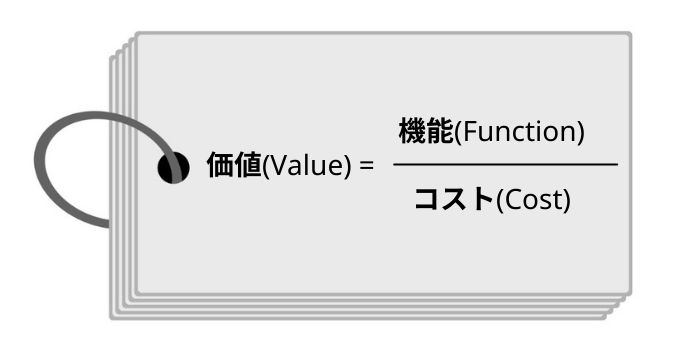
価値(Value)= 機能(Function)÷ コスト(Cost)
VE(バリューエンジニアリング)において価値を高めるために考えられる手法は主に以下の4つです。
- 手法1:同じコストで機能を向上させる
- 手法2:同じ機能でコストを削減する
- 手法3:低コストで機能を向上させる
- 手法4:コストを上げ機能をより向上させ、さらなる価値を提供する
ご紹介してきたVE(バリューエンジニアリング)の5つの基本原則と4つの手法を踏まえ、次の章では具体的な進め方を解説していきます。
VE(バリューエンジニアリング)の手順・進め方
VE(バリューエンジニアリング)の手順は、3つの基本ステップと、10の詳細ステップ、それらに付随するVE質問によって構成されます。
3つの基本ステップ
- 機能定義(分解)
顧客(ユーザー)の求める価値に関する情報の収集、必要となる機能の定義などを整理する。 - 機能評価(分析)
機能別のコスト分析と評価を行い、VE対象分野を選ぶ。 - 代替案作成(創造)
アイデア発想とその評価を行い具体化する。
10の詳細ステップ
①対象の情報収集
対象の使用・販売・設計・調達・製造・コストなどに関する情報を収集。
②機能の定義
対象から機能を抜き出して定義。対象の構成要素から、働き・役割・目的を顧客(ユーザー)目線で洗い出す。
③機能の整理
洗い出した機能を目的-手段の関係で整理する整理し、機能系統図を作成する。
④機能別コスト分析
必要とする機能の達成に費やされるコストを算出、分析する。
⑤機能の評価
機能達成に必要なコストの最低値(機能評価値)をもとに、各機能の価値の重要度を評価する。
⑥対象分野の選定
価値の程度(機能評価値/現行コスト)、コスト低減余地(現行コスト-機能評価値)を計算して、改善する機能分野の優先順位を決める。
⑦アイデア発想
③で作成した機能系統図の機能からアイデアを発想する。
⑧概略評価
発想されたアイデアを評価すると同時に、必要な機能を技術的に達成できる可能性があるか、経済面ではコスト目標の達成に貢献できる可能性があるかを評価する。
⑨具体化
概略評価されたアイデアを組み合わせ、「利点・欠点分析→欠点の克服→洗練化」の活動を根気よく繰り返し(具体化のサイクル)、アイデアを価値の高い代替案に練り上げて行く。
⑩詳細評価
練り上げた代替案の技術性・経済性の評価を行い、実際に実施する代替案を決定する。
VE質問
- ①「それは何か?」
- ②「その働きは何か?」
- ③「何のため(目的)?」「どのようにして(手段)?」
- ④「そのコストはいくらか?」
- ⑤「その価値は?」
- ⑥「その価値は?」
- ⑦「他に同じ働きをするものはないか?」
- ⑧「コストはいくらか?」「必要な機能を確実に果たすか?」
- ⑨「コストはいくらか?」「必要な機能を確実に果たすか?」
- ⑩「コストはいくらか?」「必要な機能を確実に果たすか?」
VE(バリューエンジニアリング)の手順まとめ表
3つの基本ステップ | 10の詳細ステップ | VE質問 |
①機能定義(分解) | ①対象の情報収集 | それは何か? |
②機能の定義 | その働きは何か? | |
③機能の整理 | ||
②機能評価(分析) | ④機能別コスト分析 | そのコストはいくらか? その価値はどうか? |
⑤機能の評価 | ||
⑥対象分野の選定 | ||
③代替案作成(創造) | ⑦アイデア発想 | 他に同じ働きをするものはないか? |
⑧概略評価 |
コストはいくらか?必要な機能を確実に果たすか? |
|
⑨具体化 | ||
⑩詳細評価 |
VE(バリューエンジニアリング)リーダーとは
VEリーダーとは、職場やグループでの活動において、VE活動のリーダーを務めるために必要な基礎知識をもっている人材であることを公益社団法人日本バリュー・エンジニアリング協会が実施するVEリーダー認定試験で認定されます。
創造力の発揮にもとづいて資源の有効活用を図るVEのさらなる普及と活用、そのための人材の育成が求められているという、社会的背景と期待のなか、VEリーダー資格は必要とされる人材の育成に貢献しています。
VEは、コストダウンのための一つの手法という効果だけでなく、課題に対して『それは何のために』という問いかけを行い、その目的と手段を分析し、創造的に問題解決にもつながることから、今後ますますVEリーダーの需要は高まっていきそうです。
VE(バリューエンジニアリング)の効果・メリット
バリューエンジニアリングの手法でもご紹介しましたが、
- 同じコストで機能を向上させる
- 同じ機能でコストを削減
- 低コストで機能を向上させる
この3つを実行することで、以下のような効果やメリットが生まれます。
- 全体的なコストの削減
- 設計や生産・製造の効率化
- 顧客(ユーザー)の満足度アップ
- 事業・製品のクオリティやスタッフ(社員)の技術力・創造力アップ
- 組織(チーム)のコミュニケーションの円滑化、チーム力の向上
- ミスや問題の未然防止・原因の早期究明
VE(バリューエンジニアリング)の事例
公益社団法人日本バリュー・エンジニアリング協会には法人・団体・個人を合わせて2021年11月30日時点で259の会員が加入しています。
いすゞ自動車株式会社、パナソニック株式会社、三菱電機株式会社、東京ガス株式会社など大企業が名を連ねており、VE(バリューエンジニアリング)に取り組んでいます。
VE(バリューエンジニアリング)をサポートするIoT
新型コロナウイルス、人手不足などさまざまな問題に直面している状況下において、VE(バリューエンジニアリング)に取り組み、コストの低減、製造・管理の効率化を測ることは必須です。
そこで注目され、近年続々と各企業で導入されているのが在庫管理・発注の自動化であり、その最も有効な方法として以下の2つが大きなキーワードとされています。
● DX(デジタルトランスフォーメーション)
企業の営みや産業全体をデジタルの力でよりよくしていく取り組み
● IoT(Internet of Things)
IoT=「モノのインターネット化」
IoT機器を導入することにより、「自動化」や「見える化」が可能になり、棚卸、現場作業の改善、在庫管理、発注管理、品質管理なども効率的に行えるようになります。
このように稼働状況や生産状況、在庫などのデータを分析することで、人力では発見しにくい問題や傾向なども把握できるようになり、生産性の向上やロスタイムの削減につながります。
デジタルテクノロジーを駆使して、企業経営や業務プロセスそのものを根本的に改善していくDX(デジタルトランスフォーメーション)を実現するためにIoTは欠かせない要素となります。
次の章では置くだけで在庫の見える化が可能!今、話題のIoT機器「スマートマットクラウド」をご紹介します。
製造業の見える化・自動化を実現!スマートマットクラウド
現場のあらゆるモノをIoTで見える化し、発注を自動化するDXソリューション「スマートマットクラウド」を使えば、簡単に自動化が可能です。スマートマットの上に管理したいモノを載せるだけで設置が完了。
あとはマットが自動でモノの在庫を検知、クラウド上でデータを管理し、適切なタイミングで自動発注してくれます。
さまざまな自動発注に対応
お客様の発注先に合わせた文面でメール・FAXの送信が可能です。
在庫圧縮を促進
推移を把握できるグラフで適切な在庫量を判断し、在庫圧縮を促進します。
置く場所を選びません
スマートマットはA3サイズ〜A6サイズまでの4サイズ展開。ケーブルレスで、冷蔵庫・冷凍庫利用も可能。
API・CSVでのシステム連携実績も多数
自社システムや他社システムと連携を行い、より在庫管理効率UPを実現します。
リアルタイム実在庫のデータを収集、分析、遠隔管理が可能
スマートマットクラウドはリアルタイム実在庫のデータを収集、分析、遠隔で管理。工場内の自動化、スマートファクトリー化をサポートするIoTソリューションです。
IoTで現場のモノの動きを捉え在庫管理を自動化、その上で工程内のモノの流れを分析し問題を見える化します。さらにリアルタイム実在庫データを武器に工程を跨ぐ流れの澱みを特定しDX、現場力の向上に寄与します。
在庫置場に出向くことなくリアルタイムで管理画面から部品と仕掛品の在庫数を確認できます。在庫確認や補充タイミング把握のため、倉庫や工場内を走り回る必要はもうありません。
スマートマットクラウドは生産工程の進捗状況も可視化。
後工程からひとつ前の工程に、必要な部品を、必要なタイミングで、いくつ必要かを自動で伝えることで、製造業の生産プロセスに潜むさまざまな課題を解消します。
AI x IoTで在庫最適化をし続けられる
スマートマットは、最新データ(入出庫の理論値ではなく、現場の実数データ)を溜め続けます。
そして、その大量データをAIが監視・解釈・検知。問題をタイムリーに抽出して改善を提案するので、常に在庫の最適化をし続けることができます。