在庫管理術
OEM×在庫管理【意味や受委託双方のメリット・デメリット、ODMとの違いや供給資材の管理課題とは?】
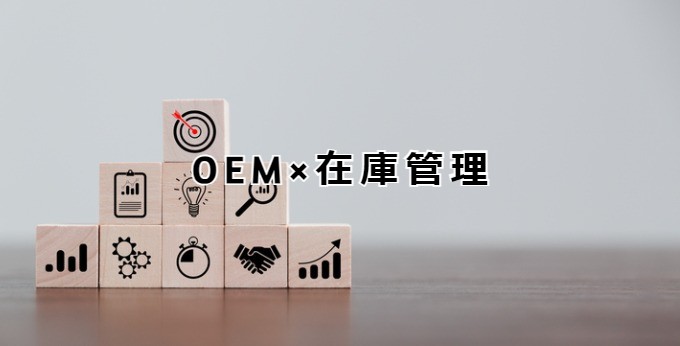
この記事では、OEMの意味やODMとの違い、メリットやデメリットについて解説します。また流出・紛失・転用すると大きな信用問題となる委託先からの供給資材の在庫管理に有益なシステムを紹介しているので、在庫管理の課題解決にぜひ役立ててください。
OEMとは?わかりやすく解説
OEMとは製造業において受委託契約を交わした生産形態のひとつ。英語では「Original Equipment Manufacturer」と言い、それぞれの頭文字を取って「OEM」や「OEM生産」と呼ばれています。
具体的に言うと、受託側のメーカーが委託側のブランド製品を代わりに生産することです。委託企業は生産を受託メーカーに任せ、主に開発や企画、販売に注力します。
ただし前後の工程や最終工程、組立・組付・裁断・小分け・パッケージ作業を委託企業や他社受託メーカーが行うことがあります。このように企業間に渡って生産工程が細分化されているケースも見受けられます。
OEMにおける垂直的分業と水平的分業
OEMにおける垂直的分業と水平的分業とは、生産技術レベルにおける委託側と受託側の関係性によって区分されます。
委託側の生産技術レベルが高く、技術的なサポートや装置・検査機の導入を行う場合は「垂直的分業」とされ、生産技術やノウハウがトップダウン的に共有されます。しかしこの場合、受託側は「下請け」のようなポジションと見なされる可能性も否定できません。
一方で委託側と受託側の生産技術レベルが同等の場合、互いの生産技術やノウハウを活用して生産するため、「水平的分業」に区分されます。
ただしこのケースでは、受託側は生産技術やノウハウの流出に拒否感を抱くことがあります。その際には委託側の人間を生産現場に立ち入らせない、指定された生産条件や4M変更*1・ISO9001*2に関連した情報以外は開示しない、という対策が執られます。
*1:4M変更とはMan(人)、Machine(機械)、Material(材料)、Method(方法)を変更した場合、管理・見える化し、BtoBに関しては一定の報告義務があるもの
*2:ISO9001とは品質マネジメントに関する国際的な共通規格
OEMとODMの違い
OEM|委託側が製品を設計・企画している
アパレルや化学・化粧品分野で一般的なのが、委託側が製品の設計・企画を行い、製造のみ受託メーカーに委ねているOEMです。この際、資材調達や良品の判断、設計段階から生産プロセスに落とし込む試作や生産立ち上げの主導権は委託側にあります。
委託側の技術力が高ければ、生産技術や技術ノウハウを提供したり、さらには必要な設備や装置を導入したりするケースも。設備や装置は状況に応じて、委託側が購入することもあれば、受託側が購入する場合もあります。
ただ当然ながら委託側が購入した場合、その設備や装置は委託企業の製品生産にしか使用できません。また委託側の責任者が受託メーカーに赴き、試作や生産の立ち上げ段階、品質チェックなどに立ち会うことも数多く見受けられます。
またここ最近の化粧品分野では、ネット販売の普及により個人経営者や小規模販売者が増えたため、企画から受託メーカーと共同で行うケースが増えています。その場合は受託メーカーが委託側の要望をくみ取る形で製品を設計し、薬機法*3や景表法*4に基づき販売ノウハウを教授することもあるようです。
*3:薬機法とは、医薬品・医薬部外品・化粧品・医療機器・再生医療等製品を規制対象とし、これらの品質、有効性、安全性を確保することにより、保健衛生の向上を図ることを目的とした法律。(厚生労働省の医薬品、医療機器等に関する法律より)
*4:正式には景品表示法。企業が商品・サービスを提供するにあたって「消費者を誤認させるような不当な広告をすること」「消費者の判断を誤らせるような課題な景品の提供をすること」を厳しく規制した法律。(消費者庁の景品表示法により)
ODM|受託側が製品を設計・企画している
ODMとは「Original Design Manufacture」の略で設計・企画から受託メーカーが行う受託生産です。例えば、受託側が製品を設計・企画し、大きな販路を持つ企業に「御社のブランド名で販売しませんか?」と提案します。
委託側は自社のブランドイメージに適し、品質や供給に問題なく、また販路をうまく使って十分な利益を見込めるならば生産を依頼します。ODMの場合、資材調達から生産立ち上げなど主導権は受託側にあり、技術水準も受託側が委託側より高い、少なくとも同等であることが基本です。
食品や日用品の小売業では、パスタや調味料・ソース・加工食品などがスーパーのオリジナルブランドとして販売されていますが、製造所を確認すると有名な食品メーカーの工場名の記載が見受けられます。
こういったものの多くは、受託側が製品を設計・企画しているODMに当てはまります。実際に自動車産業でもODMが多く、軽自動車が得意なダイハツがトヨタの軽自動車、ピクシスシリーズを生産していることは有名です。
またアパレル業界の受託生産はOEMが主流だと思われがちですが、意外にもデザイン設計から任せるODMも活躍。実は、アパレル業界は数年単位で流行を「計画」することで、紡績・染色・織布・プリント・パターン・縫製・装飾*5・検品の何段階にも渡る長い生産リードタイムをクリアしていると言われています。
自己表現のひとつであるファッションではあるものの、少なくともODMの場合、販売側はブランドイメージや自己表現に重きを置くより、短いサイクルで商品化し、販売するという点を重視しています。
*5:刺繍やブランドロゴ入れ、タグ・ワッペン・レース・飾り縫いなど
OEMのメリット
OEMには受託側・委託側の双方に次のようなメリットがあります。
受託側のメリット
- 工場稼働率の底上げが可能
- 開発・試作・生産立上げに掛かる費用は委託側が負担
- 生産技術力やノウハウの向上、蓄積*6
- 新しい設備や装置・検査機器導入の契機
受託側の最大のメリットは自社オリジナル商品が少なくても、工場の稼働率が上げられる点です。また受託規模によっては8時間稼働から交代制の24時間稼働に移行するなど、工場の生産高そのものを底上げできます。
さらにオリジナル商品であれば、開発や試作・生産プロセスへの落とし込みに掛かる時間や費用は自己負担しなくてはなりません。しかし他社製品のOEMの場合、これらは基本的に委託側が負担します。
次いで委託側の生産技術レベルが高かったり、新しい技術や装置・設備に造詣が深かったりする場合、こういった技術やノウハウをいわば無償で教授することが可能です。委託側も生産に必要な技術は受託側に提示する必要があるため、出し惜しみすることはありません。
最後に受託生産に必要な新しい設備・装置・検査機器の導入のきっかけになるのも有益なメリットです。工場や企業の上層部にとって、自社商品のためだけに新しい設備等に資金を出すかは悩みどころであっても、受託生産に必要なら資金を出す*7ハードルは低くなるでしょう。
*6:委託側の技術レベルが高い垂直的分業の場合
*7:高額な設備等の場合、まず委託側に資金を出してもらい、受託した生産物の料金から一定額を月賦返還し自社所有の設備とする場合もあります。
委託側のメリット
- 自社対応が不可な製品の生産が可能
- 工場稼働率や全体生産高は自社損益に無関係
- 必要な時のアウトソーシングを確保
- シンプルな増産なら生産移行もスピーディ
工場規模の生産体制がない、または新規開発製品に対応できる生産ラインを保有してなくても、受託メーカーで試作や生産できる点が委託側にとって最たるメリットです。
高いクリーン度の維持や重量物の自動搬送が可能な生産環境か、希望の製品規格に対応できる生産ラインか、熟練工による品質保持が可能かなど、受託側の生産能力の見極めは必要です。
しかしこれらの条件をクリアし、生産プロセスへの落とし込みも完了すれば、生産は受託メーカーに任せ、委託側は再び新規製品の開発に注力できます。
さらに受託メーカーの稼働率や生産高は委託側の損益には影響しません。ただし健全な契約継続のためには、受託依頼のある時だけメーカー側が生産体制を大幅に変更したり、残業続きになったり、僅かな利益しかなかったりするのはNG。余裕を持った納期・適切な委託料の支払いを心掛ける必要があります。
また受託メーカーと良好な関係を築けているならば、季節限定や地域限定・コラボ商品など必要な時に小回りのよいアウトソーシングとしての生産力を確保できます。
最後に自社で生産している製品でも、さらに需要が見込まれるなら、新たに工場や生産ラインを増設するよりOEMを採択するという手段があります。工場増設や増員スタッフへの教育に掛かるリードタイムと費用がカットできるため、短期間・低コストでの増産体制の構築が可能です。
OEMのデメリット・注意点
OEM生産には受託側・委託側に次のようなデメリットや注意点があります。
受託側のデメリット
- 不良品を出した際の責任所在の決着が困難
- 生産技術やノウハウの流出
- 技術刷新や現場改善・カイゼンが受け身
- 生産量のコントロールが困難
- 自社製品の生産や開発品の生産立ち上げを圧迫
不良品を出してしまった場合、責任の所在が不明になることがあります。一般的には生産している受託側に責任がありますが、想定外のトラブルが起こった場合、製品の設計内容に要因があることも。しかしながらそれを受託側が証明するのは極めて難しく、また委託側も非を認めることはほぼありません。
またOEMの契約内容は、基本的に製品数量に対価を支払います。しかし加工条件がかなりシビアな場合、ライン動作開始までに初期点検や清掃の時間を大幅に採ったり、チョコ停*7を繰り返したりすることも。その際には、時間や日数単位で受託側に対価を支払う契約内容となる場合があります。
こういった日数対価の契約内容となっても、良品ありきの請求・支払いが基本です。そのため不良品が出た場合の有責を決めることは、設計不備であっても難しく、どうしても受託側の立場は弱いというのがデメリットです。
また前述の通り「水平的分業」の場合、受託メーカーの生産技術やノウハウが流出することも。最悪の場合、その技術やノウハウを用いて競合他社に受託生産を移行されてしまうことがあります。
一方で「垂直的分業」の場合、新しい技術や装置に関する知見を得ることは容易くなります。そのため却って、技術者は自発的に新しい技術や装置の知見を得ること、生産管理者や現場スタッフは現場の改善・カイゼンすることに疎くなる傾向があります。
また受託生産量の増減によって、日々の生産量のコントロールに影響が出てきます。突発的な納品依頼は自社製品の生産を圧迫したり、逆に急に減量された場合は工場稼働率の低下に直結する点がデメリットです。
受託製品が工場の生産割合を大きく占めている場合、自社製品に使える時間が少なくなります。そのため自社ブランドの生産だけでなく、新規開発品の生産プロセスへの落とし込みにも十分な時間を割けません。OEMに偏りすぎると自社商品の弱体化に繋がる可能性にも注意しましょう。
委託側のデメリット
- 不良発生時の原因究明が困難
- 自社の生産技術向上の阻害
- 自社工場への利益還元はゼロ
- 受託メーカーが脅威となる競合化
委託側のデメリットとしては、生産時に不良が発生した際に原因究明が困難となることです。生産ラインに異常があったのか、原材料に異常があったのか、製品設計に無理があったのか、受託メーカーからの報告だけでは判断が難しい場合があります。
こういったことを防ぐために生産時に毎回、委託側の人間が良品判断に立ち会うことがあります。しかしよほどの信頼関係、もしくは完全な垂直型分業でもない限り、生産現場内に隈なく立ち入ることは難しい側面があります。
そのため、自社生産なら可能な不良品発生時の原因究明・分析・改善といった道筋を辿れません。単純に良品もしくは不良品判断にのみ立ち会っているため、根本的な問題解決に至らない場合があります。
また自社に生産設備があったとしても、コスト面やスタッフの熟練度などでOEMを選択し続けた場合、自社の生産技術の向上を阻害します。また生産に関わる費用はまるっと受託メーカーに支払われるため、自社工場やそこに携わるスタッフへの利益還元はありません。
最後に、OEMの初期段階では垂直的分業であったとしても、徐々に受託メーカーの技術力が上がり、競合化する場合も。受託メーカーが数多くの企業とOEM契約をしていれば、更に生産技術が集約化・先鋭化され大きな脅威となります。
場合によっては、特許に抵触しない範囲での代替品を割安で生産され、市場に参入されることにも留意しなくてはいけません。
関連記事>>製造業の改善・カイゼンとは?違いやトヨタ式カイゼンを紹介
OEMの課題×在庫管理|供給資材の区別・流用防止
OEMの受託メーカーが抱える課題として、供給された資材の在庫管理の難しさが挙げられます。というのも、自社製品と分野が全く異なる製品の生産を委託されることは、まずあり得ないからです。
そのため自社製品の原材料や副資材と非常に類似、または全く同じものを供給される可能性があります。同じ原材料・サプライヤーでも、委託企業と自社では購入価格が異なる、委託先が原材料のロット指定をしている、というケースも否めません。
従って、自社製品用の原材料と委託企業から供給された原材料の混流を防ぐ必要があります。しかしながら倉庫スペースが限られていたり、危険物や毒劇物であった場合にはそれぞれの法律*8で置き場所が定められていたりします。
結果的に、同じ場所での保管・同じ倉庫や棚からの出庫といったオペレーションが必然となります。しかしそれが混流を引き起こす要因となるため、委託企業から供給された資材の在庫管理には常に課題があります。
*8:危険物は「消防法による危険物の規制に関する規則」による。毒劇物は「毒物および劇物取締法」による。
IoT重量計でOEM在庫を管理
重さで数や割合をカウントし、上位システムに自動でデータを送信するIoT重量計在庫管理システム。これを活用してOEM供給資材の在庫管理をすれば、煩雑できめ細やかな配慮が必要な供給資材の管理工数を大幅に削減することが可能です。
供給資材とIoT重量計を紐づけるだけでOK。アプリからの初期設定が可能なので供給資材が入荷次第、すぐさま上位システムに登録できます。あとは重量計に管理したい資材や副資材を載せておけば、遠隔で在庫数の確認が取れます。
さらに重量データの変動をリアルタイムで捉えるため、必要以外の出庫もいち早く検知。またアプリで商品バーコードやIoT重量計のシリアルNoを読み取ることで入出庫・在庫管理も可能です。誰が・いつ持ち出したかも可視化できるため、供給資材の流用や混流を防ぎます。
遠隔からの一元管理、リアルタイム管理が可能なため、供給資材の在庫確認や入出庫チェック、自社製品の資材と混流していないか確認するために工場内を走り回る必要はもうありません。
リアルタイム在庫管理を武器に顧客資材の紛失・流用を防ぐ!「スマートマットクラウド」
現場のあらゆるモノをIoTで見える化し、発注を自動化するDXソリューション「スマートマットクラウド」を使えば、在庫管理の自動化が可能です。スマートマットの上に管理したいモノを載せるだけで設置が完了。
あとはIoT重量計が自動でモノの在庫量(個数/%)を検知、クラウド上でデータを管理します。さらに過去の発注履歴や在庫変動を基に、最適な発注点や閾値をレコメンドし適正在庫の維持に貢献。適切なタイミングで自動発注や発注アラートができます。
初期設定や入出庫管理が可能なスマートマットクラウドのHandy Appを使えば、資材や副資材の入荷次第に、上位システムへの登録が可能。委託企業から供給された資材や副資材の在庫管理にスマートマットクラウドシステムを使うことで、大幅に工数を減らし、自社製品の資材との混流防止に寄与します。
●さまざまな自動発注に対応
お客様の発注先に合わせた文面でメール・FAXの送信が可能です
●在庫圧縮を促進
推移を把握できるグラフで適切な在庫量を判断し、在庫圧縮を促進します
●置く場所を選びません
スマートマットはA3サイズ〜A6サイズまでの4サイズ展開。ケーブルレスで、冷蔵庫・冷凍庫利用も可能。
●API・CSVでのシステム連携実績も多数
自社システムや他社システムと連携を行い、より在庫管理効率UPを実現します。
●リアルタイム実在庫のデータを収集、分析、遠隔管理が可能
スマートマットクラウドはリアルタイム実在庫のデータを収集、分析、遠隔で管理。工場内の自動化、スマートファクトリー化をサポートするIoTソリューションです。
在庫置場に出向くことなくリアルタイムで管理画面から在庫数の確認が可能。顧客からの供給資材の確認や混流防止のため、わざわざ現場確認に行く必要性が低くなります。
◆特徴
- 在庫管理工数削減:日次での在庫確認と発注を自動化。リモート管理もOK!
- 欠品・過剰在庫防止:自動発注機能の活用で適正在庫を維持
- 在庫差異を縮小:重量計測で正確な在庫数を自動記録
- 遠隔かつリアルタイムで一元管理:倉庫や各拠点の在庫や入出庫状況を可視化、管理