在庫管理術
バッチプロセス生産【バッチの意味や生産管理の特徴と課題、解決方法を解説】
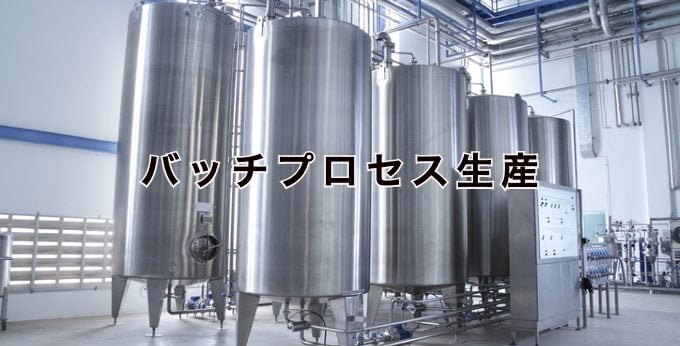
製造業において食品・医薬・化学・石油化学・セメント・鉄鋼などの業種では「プロセス製造」が主な製造手段となります。このプロセス製造には、連続プロセスとバッチプロセスとがあります。
今回はバッチプロセスの特徴と、バッチプロセス製造が抱える課題、その解決方法について紹介します。
バッチプロセスとは?
そもそもプロセス製造とは、熱や圧力による状態反応や分解反応、もしくは化学反応や合成によって原材料を変容させて製品をつくる手段です。
その中でも同一の設備や装置内で、工程や製品単位で区切って原材料をまとめて投入し、出来上がれば装置を停止し、再び原材料を入れ替え別の工程や製品の加工を繰り返す製造形態を「バッチプロセス」と言います。
バッチプロセスは、多品種少量生産に適していて、医薬品、食品、化学品で用いられる生産プロセスです。
バッチプロセスと連続プロセス
バッチプロセスと対になる製造形態を「連続プロセス」といいます。
常に装置を稼働させておき、原材料を連続的に投入し継続して処理を行います。
処理中は同じ原材料を投入し続け、主剤と副剤などの配合比率も調整程度にしか変わりません。
石油化学、セメント、鉄鋼業で主に採用されている生産プロセスで、バッチプロセスに比べてオペレーションが簡潔なため、産業用ロボットや遠隔操作による自動化を推進しやすいという特徴があります。
そもそもバッチとは
「バッチ」とは、生産現場では「ある程度の量をまとめて生産・加工すること」をいいます。「1回分」という意味をもつ英語「Batch」がその語源となっています。
プロセス製造における釜や炉、調合タンク1回分の生産量は、「1バッチ」、「2バッチ」とカウントされます。
バッチプロセスの特徴
高度な管理が必要
バッチプロセスでは、同一の設備で多品種の生産をおこないます。製造物によって、レシピを切り替える必要があるため、連続プロセスと比較すると精密な管理が要求されます。
具体的には
- レシピ通りの原材料をピッキング
- 原材料の正確な計量
- 原材料の正確な投入
が求められます。
手動の作業が多い
バッチプロセスはレシピや工程の切り替えのたびに設備に原材料を投入し、製造物の取り出しをするため、人が設備の周りに在中し、作業する時間が長くなります。連続プロセスよりも効率化をすすめにくいという特徴があります。
製造のやり直しができない
バッチプロセスでは、1バッチ分の原材料を装置に投入し、反応や合成によって原材料を変化させます。製造過程でトラブルが起きた場合、ほとんどのケースでやり直しが効かず、1バッチ分のすべての原材料がロスとなります。
また反応や合成には一定時間を要するので、不良品が発生すると生産スケジュールにリカバリーと変わらない時間分の遅れが生じます。
バッチプロセスの課題
ピッキングミス
人の手による投入や取り出し作業が発生するバッチプロセスの課題に、原材料のピッキングミスがあります。通常、プロセス製造では事前に倉庫から装置付近までレシピ通りに原材料をピッキングし運搬しておきます。
レシピは工程によって異なり、ピッカーの見間違いや勘違いが原因で本来必要な原材料と異なる資材をピッキングしてしまうことがあります。
計量ミス
プロセス製造では設備に投入する前に材料をレシピ通りに原材料を計量します。そもそもプロセス製造で使用する原材料や添加物は、液体や粉末の形状であることが多いため、配合表の見間違いや単純な計算ミスにより計量ミスが引き起こされやすいという課題があります。
投入ミス
計量した原材料を設備に投入する段階でも、人為的ミスは発生します。原材料の一部を投入し忘れる、こぼしてしまうなどのトラブルに見舞われることがあります。
重さの自動計測でバッチプロセス特有の誤生産を回避
工程管理DX「スマートマットクラウド」は、こうしたプロセス製造特有の「レシピずれ」の課題を解消することができます。
重量IoTが搭載されているスマートマットを原材料の仮置場や投入口に設置して、投入前の原材料を固定ロケーションで管理すると、重さから以下のポイントを自動で確認できます。
- 正しく原材料がピッキングされているか
- 正確に原材料が計測されているか
- もれなく原材料が投入されているか
人為的ミスによるトラブル発生や、製造コストへの悪影響を回避することが可能です。
バッチプロセス生産を「スマートマットクラウド」でカイゼン
「重さ」のデータをリアルタイムに共有するIoT重量計を用いたスマートマットクラウドは、原料のピッキングミス・レシピずれの早期発見に寄与します。
現場スタッフと生産管理とでデータを共有してミスの指摘を的確に行い、業務プロセスを改善。これまでシンプルな生産体制の構築が困難だったプロセス製造のDX推進を強力にサポートします。
◆特徴